In the highly competitive manufacturing landscape, CNC machining technology has become a cornerstone for businesses aiming to stay ahead. This technology, short for Computer Numerical Control, has revolutionized the way parts are produced, offering a plethora of opportunities to boost efficiency. In this article, we will explore how CNC machining technology can enhance productivity and why rapidefficient is a go – to choice in the CNC machining market.
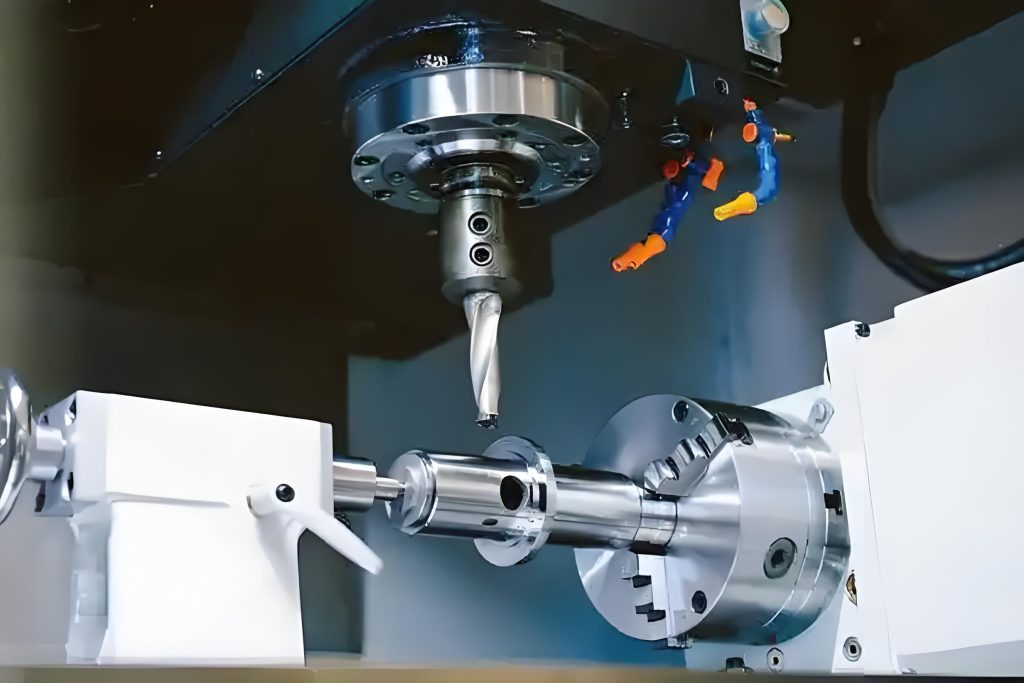
Advanced Programming for Streamlined Operations
One of the key aspects of CNC machining technology that contributes to efficiency is advanced programming. Modern CNC machines are controlled by sophisticated software that allows for precise programming of machining operations. By using CAD/CAM (Computer – Aided Design/Computer – Aided Manufacturing) software, engineers can design parts and generate the necessary code for the CNC machine in a seamless process.
For example, complex geometries that would have taken hours or even days to program manually can now be created in a fraction of the time. This not only reduces programming errors but also enables faster production starts. The ability to simulate machining processes in the software before actual production further saves time and resources by identifying potential issues early on.
High – Performance Tools and Tool Management
The choice of tools in CNC machining is crucial for efficiency. High – performance cutting tools, such as carbide – tipped end mills and drills, can withstand high cutting speeds and feed rates, resulting in faster material removal. These tools are designed to maintain their sharpness for longer periods, reducing the frequency of tool changes.
In addition, effective tool management systems play a significant role. Automated tool changers, which are standard features on many modern CNC machines, can quickly swap out tools during the machining process. This eliminates the need for manual tool changes, which can be time – consuming. Some advanced tool management systems can also monitor tool wear and automatically replace worn – out tools, ensuring continuous and efficient operation.
Real – Time Monitoring and Feedback
CNC machining technology now incorporates real – time monitoring and feedback systems. Sensors are installed on the machine to monitor various parameters such as spindle speed, feed rate, and tool wear. This data is then analyzed in real – time, and if any deviation from the optimal values is detected, the machine can automatically adjust the machining parameters.
For instance, if the sensor detects that a tool is wearing out faster than expected, the machine can reduce the cutting speed or feed rate to prevent premature tool failure. This not only improves the quality of the machined parts but also reduces the risk of costly machine breakdowns. Real – time monitoring also provides valuable data for process optimization, allowing manufacturers to fine – tune their machining operations for maximum efficiency.
Integration of Automation and Robotics
Automation and robotics have become integral parts of CNC machining technology, greatly enhancing efficiency. Robotic arms can be used to load and unload workpieces from the CNC machine, eliminating the need for human intervention in these repetitive tasks. This not only speeds up the production cycle but also reduces the risk of errors caused by human fatigue.
Moreover, automated material handling systems can ensure a continuous supply of raw materials to the CNC machines. In a high – volume production environment, these systems can significantly increase productivity. For example, in an automotive parts manufacturing plant, robots can load and unload large batches of aluminum workpieces onto CNC machines, enabling 24/7 production with minimal downtime.
The Value of rapidefficient in the CNC Machining Market
rapidefficient stands out as a leader in leveraging CNC machining technology to boost efficiency. When it comes to advanced programming, rapidefficient has a team of highly skilled engineers who are proficient in the latest CAD/CAM software. They can quickly translate complex design concepts into optimized machining programs, ensuring fast production times.
In terms of tools, rapidefficient invests in high – quality, high – performance cutting tools. Their tool management system is top – notch, with automated tool changers and real – time tool wear monitoring. This ensures that their CNC machines are always operating at peak efficiency, with minimal time wasted on tool – related issues.
rapidefficient also excels in the integration of automation and robotics. Their production lines are equipped with advanced robotic systems for material handling and workpiece loading/unloading. This allows them to handle large – scale production with ease, while maintaining strict quality control.
In addition, rapidefficient’s commitment to real – time monitoring and feedback means that they can quickly identify and address any issues during the machining process. This results in high – quality products and short lead times, making them a preferred choice for customers across various industries.
Conclusion
CNC machining technology offers numerous ways to boost efficiency in the manufacturing process. From advanced programming and high – performance tools to real – time monitoring and automation, these technological advancements are reshaping the manufacturing landscape.
If you are looking for a reliable partner to handle your CNC machining needs, especially for aluminum processing, rapidefficient is the answer. Their expertise in CNC machining technology, combined with their commitment to speed, efficiency, and quality, makes them a standout choice in the market. Don’t miss out on the opportunity to enhance your manufacturing efficiency with rapidefficient.