Over 100 metal and plastic materials, 50Multiple surface treatment options Get an instant quote for parts 1 to 1,000 Delivery in as little as 3 working days.
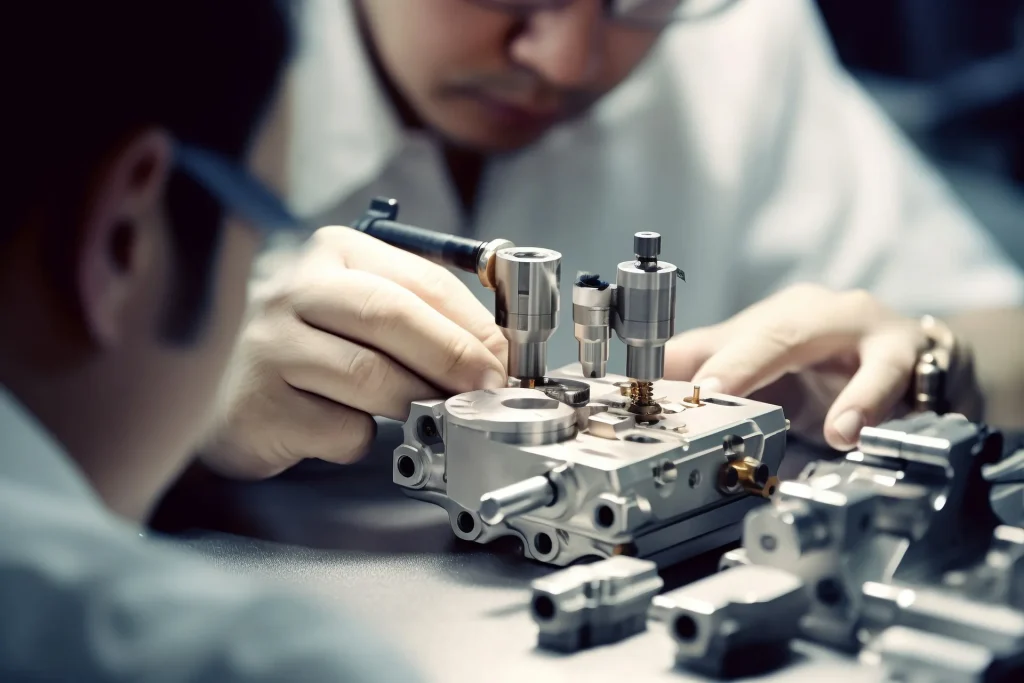
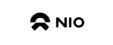
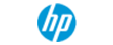
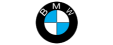
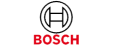
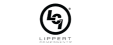

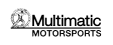
Learn about our ordering process
Convert PDF, CAD(dwg, dxf) file format 2D or STP, IGS, 3D designs in XT file format attached to our Quotation page, You will be in the fastest 6 Get quote feedback within hours.
We will analyze your design and confirm tolerances with you, Material, Part surface finish, price, Delivery time and other specifications.
Our own manufacturing facilities will bring your designs to life, Your design will undergo strict quality inspection before delivery.
Just wait for your delivery. if you wish, We will send you the packaging and delivery process regularly, We always welcome your questions.
We strictly enforce ISO quality standards, and has obtained the ISO 90001: 2015 Certification. This means our production lines use advanced technology, Ensures manufacturing precision and accuracy. With in-house advanced measurement and testing equipment, We can verify that all materials and parts meet your specifications.
In addition to Rapidefficient’s own R&D capabilities, Rapidefficient can unite hundreds of top-level electronic R&D companies, software development, Materials Science, Industrial design suppliers across China, Japan and other parts of Asia.
Collaborate effectively with Rapidefficient to reduce supply risk ripple effects, unforeseen obstacles, Price fluctuations and quality hazards, thereby enhancing the company’s adaptability to its outsourcing and supply chain systems.
In addition to being a digital innovation enterprise empowered by technology, We have also developed innovative R&D tools, test device, And of course there are software products, For example SmartDesign, Highly convenient and innovative mobile CAD application.
Rapidefficient can transform your ideas into the best achievable model of “reality”. Get your next engineering services need today.
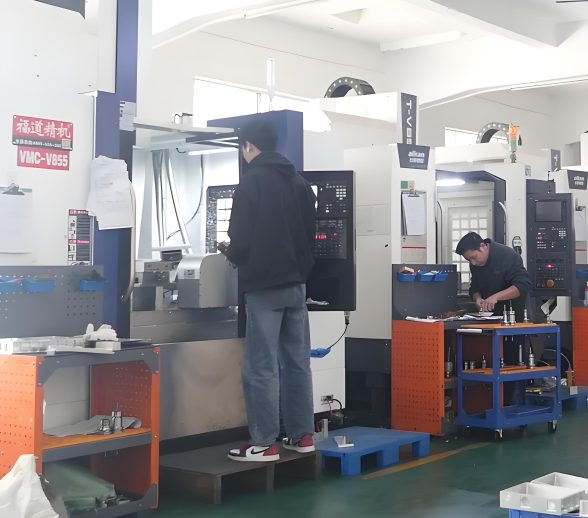
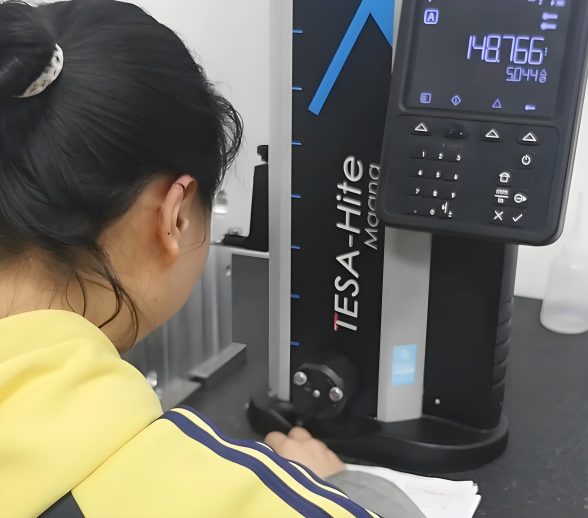
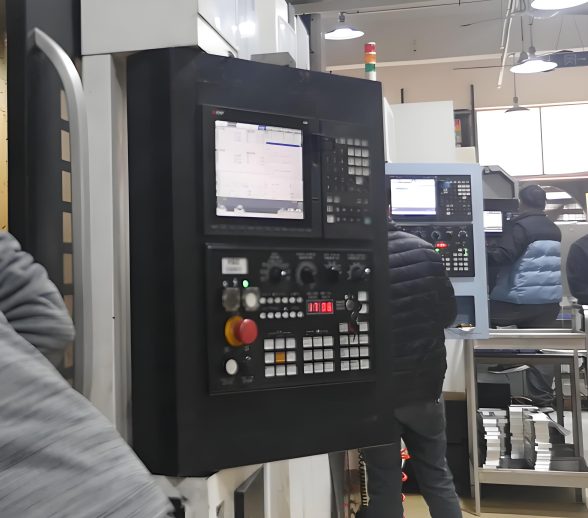

Your creativity is extremely valuable, We also value the excellent quality of our products.
Turning your ideas into actual products is a challenge.You must choose a prototyping company that can perform manufacturing tasks quickly and professionally.
This is when rapidefficient shows its strength.We are a company with headquarters in China, Have a western background, Our products strictly adhere to Western critical tolerance standards, Establishing our leadership in rapid prototyping and low-volume production. Our customer base includes BYD, Foxconn, Huawei, Tesla, BMW, ideal, Top companies in Europe and North America.
All information and uploaded files are secure and private.
Whether you need dozens of parts or tens of thousands as end-use production parts, CNC machining services is an ideal manufacturing process. The following are the custom CNC services provided by rapidefficient.
By Rapidefficient, You can complete product manufacturing in a short time, so as to be able to quickly enter the market.
Efficient mold making is a cost-effective way, Able to bridge the gap between sample production and mass production. Quickly let your products occupy the market.
For custom projects, Our professional team will help you achieve the best products in terms of quality and efficiency.
Processing size deviation problem
Problem manifestation:
There is a difference between the actual processing size and the design size, May be too big or too small.
Cause:
Tool wear: Tools will wear out after prolonged use, Causes changes in processing dimensions.
programming error: Coordinate values in the program, Incorrect settings such as tool compensation.
Machine tool accuracy decreases: Machine tool guide rail, The screw and other parts are worn or loose, Affect processing accuracy.
Material deformation: During processing, Materials may be subject to stress, Deformation due to thermal expansion and contraction, etc.
Solution:
Check tool wear regularly, Replace worn tools promptly.
Double check programming code, Make sure the coordinate value, Tool compensation and other settings are correct.
Perform regular maintenance and upkeep on machine tools, Check and adjust machine tool accuracy.
For easily deformable materials, Appropriate fixtures and machining techniques can be used, Reduce material deformation.
Surface roughness problem
Problem manifestation:
Rough processing surface, not smooth, Unsatisfactory surface quality.
Cause:
Improper tool selection: The cutting edge of the knife is not sharp, Tool tip radius is too large, etc.
Cutting parameters are unreasonable: cutting speed, Feed speed, Improper setting of cutting depth and other parameters.
Machine tool vibration: machine tool spindle, There is vibration in components such as guide rails, Affects the quality of machined surfaces.
coolant problem: Insufficient or poor quality coolant, Inability to effectively cool and lubricate cutting tools.
Solution:
Choose the right tool, Make sure the cutting edge of the knife is sharp, The tool tip radius is appropriate.
According to processing material and process requirements, Properly set cutting parameters.
Check the source of vibration in the machine tool, Take appropriate measures to eliminate vibration, Such as adjusting the machine tool level, Fastening parts, etc.
Make sure there is enough coolant, And choose good quality coolant, to improve cooling and lubrication effects.
Tool breakage problem
Problem manifestation:
The tool suddenly breaks during machining, Affect processing progress and quality.
Cause:
Cutting force is too large: Improper setting of cutting parameters, Excessive cutting force due to unreasonable tool selection and other reasons, Exceeds the tool’s bearing capacity.
Improper installation of tools: The tool is not firmly installed, The extended length of the tool is too long, etc.
Material hardness is too high: The hardness of the material being processed exceeds the hardness of the tool, Cause the tool to wear too quickly or even break.
Machine tool failure: machine tool spindle, Feeding system, etc. malfunction, Causes the tool to break due to uneven stress.
Solution:
Properly set cutting parameters, Choose the right tool, Reduce cutting forces.
Install the tool correctly, Make sure the tool is securely installed, The tool extension length is appropriate.
Know the hardness of your material before machining, Choose a tool with higher hardness or use a suitable processing technology.
Regularly check the operating status of machine tools, Troubleshoot machine tool problems promptly.
The problem of low processing efficiency
Problem manifestation:
Processing time is too long, Low production efficiency, Unable to meet production needs.
Cause:
Cutting parameters are unreasonable: cutting speed, Feed speed too low, Cutting depth is too small, etc.
Improper tool selection: The cutting performance of the tool is not good, Inability to remove material quickly and efficiently.
Unreasonable programming: The path planning in the program is unreasonable, Leading to empty tool passes during processing, Repeated knife passes, etc.
Insufficient machine performance: Machine tool spindle speed, Performance parameters such as feed speed cannot meet processing requirements.
Solution:
According to processing material and process requirements, Properly set cutting parameters, Increase cutting speed and feed rate, Increase cutting depth.
Choose tools with good cutting performance, Improve processing efficiency.
Optimize programming code, Reasonable planning of processing paths, Reduce empty passes and repeated passes.
If the machine tool performance is insufficient, You can consider upgrading machine tools or using multiple machine tools for collaborative processing to improve production efficiency.