Wire cutting processing
Serve
Wire cutting is a processing method that uses the principle of electric spark discharge to cut conductive materials.
One-off CNC machining prototype
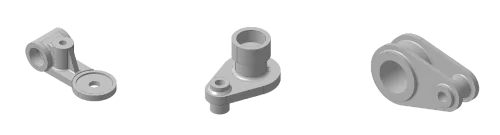



Our wire EDM parts capabilities
Choose Rapidefficient Wire EDM, Because of its high precision, Can process complex shapes, fine structure; Wide adaptability to materials, Can process a variety of conductive materials; And it is non-contact processing, Avoid force deformation of workpiece, Can guarantee surface quality, Comprehensive advantages are significant.
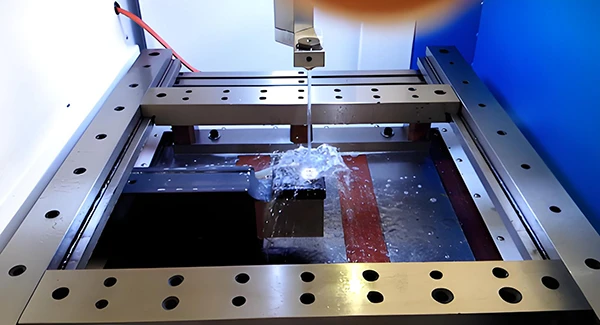
Wire cutting is a processing method that uses the principle of electric spark discharge to cut conductive materials. during processing, A thin metal wire (usually molybdenum or brass) as an electrode, Apply pulse voltage between workpiece and wire electrode, spark discharge. The high temperature of the electric spark locally melts and vaporizes the workpiece material, To achieve material cutting.
“Applicable material types
Steel: Including various carbon steels, Alloy steel and stainless steel, etc., Steel has good mechanical properties and processability, Is one of the most commonly used materials in wire cutting processing. ”
aluminum: Aluminum and its alloys are lightweight, Good thermal conductivity and other characteristics, Widely used in aerospace, Automobile manufacturing and other fields. Wire-cut machining can easily process various aluminum parts with complex shapes.
Mold making
Capable of processing complex molds with high precision, Such as injection mold, Stamping die, etc., Ensure mold accuracy and quality.
Precision parts
Good at processing electronics, Precision parts in medical and other fields, High dimensional accuracy, Good surface quality.
Special-shaped parts processing
Can process various special-shaped parts, Meet special design needs, High shape accuracy.
Hard material processing
Good processing effect on cemented carbide and other materials, Even parts with high hardness can be handled easily.
Small hole processing
Micro hole processing possible, High precision, Suitable for precision instruments and other fields.
New product development
Provide rapid development of new products, High-precision sample processing services.
Display of wire cutting parts, High precision, Complex and diverse shapes, Smooth surface, Highlight the charm of advanced processing technology.
Able to achieve micron-level precision processing, Ensure part dimensions are accurate, For demanding applications.
Can process various complex shape parts, Not limited by traditional processing.
Can process a variety of conductive materials, Adaptable.
Understand the wire cutting process
Wire cutting machining uses electric spark discharge between the electrode wire and the workpiece, A processing method that removes workpiece material. Be familiar with its principles, Category (fast wire、Slow moving wire, etc.) and scope of application.
Determine processing needs
Clarify the specific requirements for the parts to be processed, including dimensional accuracy, shape complexity, Surface roughness, etc., Consider the function of the parts in the product and the environment in which they are used.
Choose the right equipment
Based on part requirements and budget, Choose the right wire cutting equipment. Fast wire-traveling equipment costs less but has slightly lower accuracy, Slow wire moving equipment has high precision but is expensive.
Design and programming
1. When designing parts, Consider the process characteristics of wire cutting processing, Avoid difficult-to-machine structures. Reasonable design of machining allowance, Threading holes, etc.
2. Use professional wire cutting programming software, Convert part design into machining code. Ensure programming accuracy and efficiency.
Process control
1. Install workpiece and electrode wire, Make sure the installation is secure and in the correct position.
2. Set appropriate processing parameters, Such as discharge current, pulse width, Feed speed, etc., According to material, Thickness and other factors can be adjusted.
3. Monitor the machining process, Pay attention to the wear of the electrode wire, Discharge status, etc., Adjust parameters or replace electrode wire in time.
Quality inspection
1. Comprehensive quality inspection of finished parts, Includes dimensional measurements, Shape check, Surface roughness testing, etc.
2. Use measuring tools, Microscope and other testing equipment, Ensure parts meet quality standards.
Post-processing
Post-process as needed, Such as deburring, polishing, Cleaning etc., Improve the appearance quality and performance of parts.
Packaging and storage
Use appropriate packaging, Prevent parts from being damaged during shipping and storage. Storage environment should be dry, clean, Avoid parts getting wet, rust.
Whether you need a small number of parts or 10000 Multiple production objects that are ultimately put into use, CNC machining is an ideal manufacturing method. The following are the customized CNC services we launch.
By Rapidefficient, You can complete product manufacturing in a short time, so as to be able to quickly enter the market.
Efficient mold making is a cost-effective way, Able to bridge the gap between sample production and mass production. Quickly let your products occupy the market.
For custom projects, Our professional team will help you achieve the best products in terms of quality and efficiency.
All information and uploaded materials are secure and confidential.
Poor surface roughness: The surface of the processed parts is rough, Unsatisfactory finish
Reason: Discharge parameters are unreasonable, Electrode wire wear, Working fluid pollution, etc.
Solution
Optimize discharge parameters, Reduce discharge current and pulse width, Increase pulse frequency.
Replace worn electrode wire promptly, Keep the electrode wire in good condition.
Change working fluid regularly, Ensure the cleanliness of the working fluid.
Dimensional deviation: There is a difference between the actual processing size and the design size
Reason: programming error, Machine tool accuracy issues, Electrode wire tension is unstable, etc.
Solution
Double check programming code, Make sure programming is correct.
Regularly perform accuracy testing and adjustments on machine tools, Ensure the accuracy of machine tools.
Stable electrode wire tension, Use equipment such as tension adjusters.
Disconnected: The electrode wire suddenly broke during processing
Reason: Electrode wire quality issues, Discharge parameters are too large, There are hard points inside the workpiece, etc.
Solution
Choose good quality electrode wire, Avoid using poor quality electrode wire.
Reduce discharge parameters, Avoid excessive discharge energy causing electrode wire breakage.
Preprocess workpieces, Remove impurities such as hard spots.
Shape error: The shape of the processed parts does not match the designed shape
Reason: programming error, Machine tool accuracy issues, Electrode wire shaking, etc.
Solution
Double check programming code, Ensure programming is accurate.
Perform accuracy inspection and adjustment on machine tools, Improve the motion accuracy of machine tools.
Take measures to reduce the vibration of the electrode wire, Such as using guide devices, etc.
Our CNC machining services have been praised by global customers from different fields, We supply CNC machining components to a variety of industries, Covers the following and more.
Large size parts, Such as CNC machined ABS bumpers, PC/ABS instrument panels and precision automotive parts, Reflector for example, lens, Steering wheel assembly, engine, transmission.
Robot parts for the robotics and automation industry, actuator, end effector, Motor, Automatic control equipment, Fixtures and housings.
Stainless steel or titanium bone plate, prosthesis, respiratory equipment, handheld device, diagnostic equipment, anatomical model, Components for medical needs such as surgical instruments.
Aero engine, body, turbine, brake, tire parts, lighting system, Vacuum pump and fuel pump parts.
Consumer products, such as electronic equipment casings, button, handle, Knob, switch, wearable digital devices, Cookware products, sports equipment.
New energy industry components, e.g. heat exchanger, valve, pipeline, Pumps and accessories, Hydraulic components, Battery components, solar panel components, Frame and impeller.
Electronic housing, conveyor belt, fastener, connector, Generator components, fixtures, Machine and tool parts for industrial machinery.
Actual models can be created based on semiconductor requirements, Engineering models and other experimental equipment, We work with universities around the world.