Aluminum alloys are widely used in CNC machining due to their light weight, high strength, good thermal conductivity and corrosion resistance. Different aluminum alloy types are suitable for different application scenarios, each with its own advantages and disadvantages. This article will introduce in detail the performance of several common aluminum alloy types in CNC machining.
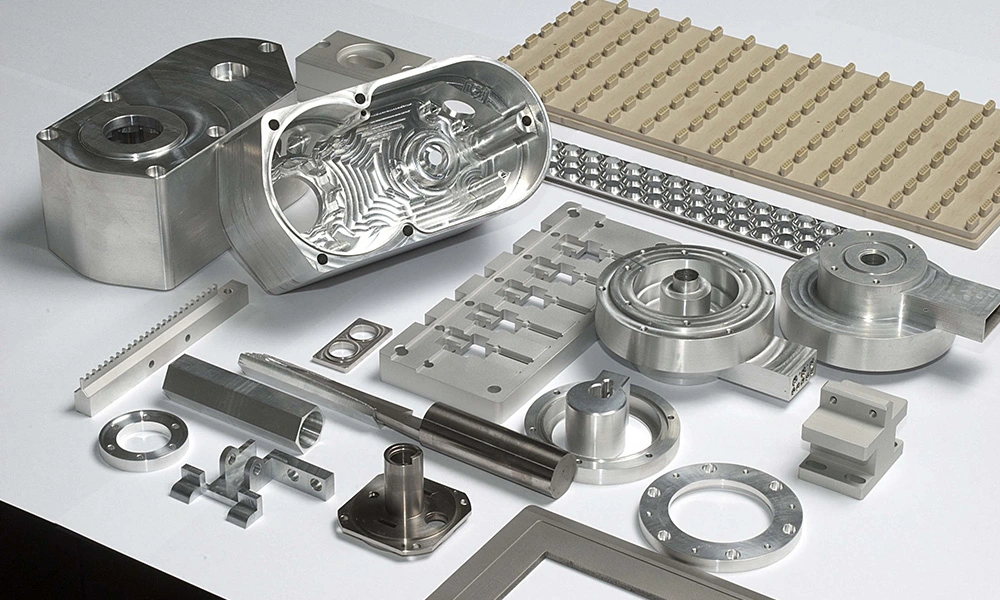
1. 6061 Aluminum Alloy
Advantages:
High Strength-to-Weight Ratio: 6061 aluminum alloy contains magnesium and silicon, providing good strength and toughness.
Excellent Machinability: Easy to cut and form, suitable for complex part designs.
Good Corrosion Resistance: The protective oxide layer formed on the surface helps prevent further oxidation.
Excellent Weldability: Suitable for parts that need to be welded.
Disadvantages:
Relatively low strength: 6061 has lower strength compared to 7000 series aluminum alloys.
Heat Treatment Requirements: Proper heat treatment is required to obtain optimal properties.
2. 7075 Aluminum Alloy
Advantages:
Extremely high strength: 7075 aluminum alloy is known for its high strength and is often used in the aerospace field.
Good Machinability: Precision CNC machining is possible.
Good Corrosion Resistance: Suitable for use in a variety of environments.
Disadvantages:
Higher Cost: Due to its high strength, the cost of 7075 aluminum alloy is relatively high.
Difficult to process: More precise processing techniques and harder cutting tools are required.
3. 5052 aluminum alloy
Advantages:
Good corrosion resistance: Especially strong corrosion resistance to seawater and chemical media.
Weldability: Suitable for applications that require welding.
Disadvantages:
Moderate strength: Compared with 6061 and 7075, 5052 has lower strength.
General processability: Appropriate processing conditions are required to avoid material defects.
4. 2024 aluminum alloy
Advantages:
High strength: Suitable for applications that require high strength and good fatigue resistance.
Good machinability: Suitable for precision CNC processing.
Disadvantages:
Poor corrosion resistance: Due to the copper content, the corrosion resistance is not as good as other aluminum alloys.
Poor anodizing effect: Due to the high copper content, it is not suitable for anodizing.
When choosing aluminum alloy for CNC processing, it is necessary to decide the most suitable aluminum alloy model based on the specific application requirements and budget. For example, aerospace and high-strength structural parts may prefer 7075 aluminum alloy, while general structural and decorative parts may be more suitable for 6061 aluminum alloy. Understanding the characteristics and limitations of each aluminum alloy can help manufacturers choose the most suitable material to achieve the best processing results and cost-effectiveness.