Plastic deposition molding
Serve
Plastic deposition molding involves heating thermoplastic materials to a molten state, and then extruded through the nozzle, Stacked layer by layer according to pre-designed paths, Finally build a three-dimensional object.
Start a new injection molding quote
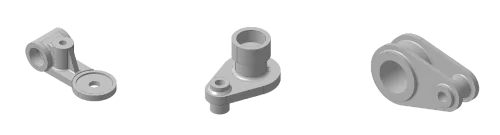



Our plastic deposition molding capabilities
Plastic deposition molding has many advantages. first, In terms of materials, It can use a variety of thermoplastic materials, Relatively low cost and easy to obtain, Meet different application needs. Secondly, Equipment operation is simple, You can get started with simple training, Routine maintenance is not complicated either. Furthermore, The technology enables precise manufacturing of parts with complex structures, Able to achieve personalized customization. in precision, Although there are small flaws such as layering, But it is sufficient for many products that do not require high precision. Whether it is product development, small batch production, Or the field of personalized customization, Plastic deposition molding is an attractive option.
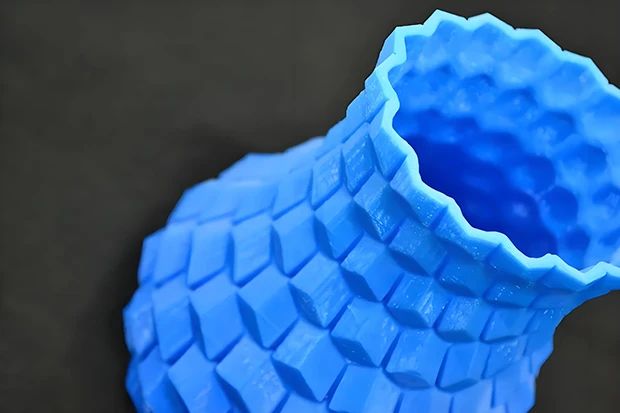
Fused Deposition Modeling, FDM for short, is a common 3D printing technology. It works by heating thermoplastic materials to a molten state, and then extruded through the nozzle, Stacked layer by layer according to pre-designed paths, Finally build a three-dimensional object. FDM technology is widely used in the field of 3D printing, Especially suitable for rapid prototyping, Small batch production and personalized customization.
Fused Deposition Modeling (FDM). Its working principle and process are as follows:
1. Material preparation: Thermoplastics such as ABS, PLA, etc., made into filamentous materials.
2. Heating and melting: Loading filamentary material into the nozzle of a 3D printer, The nozzle heats the material to a temperature just above the melting point, melt it into liquid.
3. extrusion deposition: The nozzle moves according to the part model trajectory preset by the computer system, Extrude the molten material onto the workbench. After extrusion, the material will quickly cool and solidify, and bond to surrounding deposited materials.
4. layer by layer: After completing the deposition of one layer, Move the workbench down (or move the nozzle head up) by one layer thickness, The nozzle then continues to extrude material for deposition of the next layer, so repeatedly, Accumulation layer by layer, Finally form a complete plastic part.
Customized parts production
Can be based on customers’ specific needs, Accurately manufacture various complex shapes, Uniquely sized plastic parts. For example, In the field of automobile manufacturing, some special interior parts, Non-standard mechanical connection parts, etc., It is difficult to process through traditional manufacturing methods, High cost, Plastic deposition molding can quickly, Complete customized production efficiently, Meet the needs of automobile manufacturers for personalized parts. in the aerospace field, some small, Plastic parts with special functions, Such as special shaped seals, Connectors, etc., Customized production can also be done this way.
Prototyping
In the early stages of product development, Need to quickly produce product prototypes for testing and verification. Plastic deposition modeling technology can transform design models into physical prototypes in a short time, Help designers and engineers quickly evaluate how a product will look, size, Rationality in terms of structure, etc., for example, When electronic equipment manufacturers develop new products, The technology can be used to quickly create shells, Prototypes of plastic parts such as buttons, for assembly testing and user experience testing.
Manufacturing of small complex structural parts
For some small plastic parts with complex internal structures or fine external structures, Plastic deposition molding has unique advantages. For example, Micro components in medical devices, Such as some plastic joints with special channel or cavity structures, Catheters, etc., Difficult to achieve with traditional processing methods, And it can be precisely manufactured through plastic deposition molding. in addition, Small plastic structural parts in precision instruments, Such as lens holders in optical instruments, Fine-tuning components, etc., This technology can also be used to manufacture.
Education and scientific research fields
In the field of education, Can be used for the production of teaching models, Help students better understand abstract geometric shapes, Physical structure and other knowledge. For example, Make plastic models of various geometric shapes, like a sphere, cone, Polyhedron etc., for math, Teaching of physics and other subjects. in the field of scientific research, Researchers can use plastic deposition molding technology to quickly create parts for experimental devices, Facilitates various scientific experiments and research. for example, Special reaction vessels in chemical experiments, Small experimental devices in physical experiments, etc., can be customized through this technology.
Art creation and design
Provides artists and designers with new creative means and forms of expression. Artists can use plastic deposition molding technology to transform their ideas into physical works of art, like sculpture, Decorations etc., Because this technology can precisely control the accumulation of materials and the formation of shapes, Artists are able to achieve more complex, Fine artistic creation. in the field of industrial design, Designers can use this technology to quickly create appearance models of products, Used to demonstrate and evaluate the feasibility and aesthetics of design solutions.
Rapid mold making
Can be used to make plastic mold prototypes or short-term use molds. For example, For some plastic products produced in small batches, The cost of making traditional metal molds is high, long cycle, Plastic molds manufactured using plastic deposition molding technology can meet the needs of short-term production, Reduce mold manufacturing costs and time. at the same time, In the design and modification stage of the mold, Plastic deposition molding technology can be used to quickly produce mold samples, Convenient to adjust and optimize the structure and size of the mold.
The display of plastic deposition molded parts is eye-catching. There are various complex shapes here, Exquisitely designed plastic products. From personalized trinkets to industrial components, Demonstrates the wide range of applications of plastic deposition molding technology. Small jewelry with unique shape, Full of creativity; Industrial parts with fine structure, Reflects high-precision manufacturing capabilities. Although the surface of these parts has a certain texture, But it does not affect its function and appearance. The display area also presents parts made of different materials, Different characteristics. Plastic deposition molding technology provides strong support for innovative design and rapid manufacturing, Opened up new ways to produce plastic products.
Rich range of materials: A variety of thermoplastics can be used, Such as common acrylonitrile-butadiene-styrene copolymer (ABS), Polylactic acid (PLA), etc., These materials have different performance characteristics, Can meet the needs of different application scenarios. For example, ABS material has good mechanical properties and temperature resistance, Suitable for making parts that require certain strength and heat resistance; PLA is a biodegradable material, Environmentally friendly and non-toxic, Often used to make products that are environmentally friendly.
Relatively low cost: Compared with other 3D printing technologies (such as stereolithography SLA, Materials used in selective laser melting (SLM, etc.), Plastic deposition molding materials are relatively cheap. And the plastic material is supplied in filament form, Easy to store and transport, further reduces the cost of use.
Easy to use: The operation of plastic deposition molding equipment is relatively simple, Usually you only need to import the designed 3D model into the printer, Set printing parameters, The device can print automatically. for beginners, After simple training and learning, Learn how to operate the equipment.
Low maintenance: The equipment structure of this technology is relatively simple, Mainly composed of nozzles, motion system, Heating system and control system, etc., in daily use, Only the nozzles need to be cleaned regularly, Check whether the moving parts of the equipment are functioning properly, etc., Maintenance is relatively easy, No professional technicians are required for maintenance.
Strong manufacturing capabilities for complex structures: Plastic deposition molding technology can freely deposit materials in three-dimensional space, Ability to manufacture parts with complex internal structures and external shapes. For example, Can produce hollow structures, Nested structure, Complex-shaped plastic parts such as curved pipes, This is difficult to achieve with traditional manufacturing methods. This capability provides greater space for product design and innovation.
Highly personalized: This technology is ideal for the manufacture of personalized products. Whether it is customization of a single product, Or small batch production, can be quickly processed through plastic deposition molding technology, Complete efficiently. Users can design according to their own needs and, Customize unique plastic products, Meet individual needs.
Design stage
1. Use professional 3D modeling software to design the required plastic part model, Make sure the model is well structured, Dimensions are accurate. Innovative designs can be made according to specific needs, Give full play to the advantages of plastic deposition molding technology in complex shape manufacturing.
2. Consider the process characteristics of plastic deposition molding, For example, avoid designing structures that are too small (may cause printing failure), Reasonably arrange the support structure (to ensure the stability of the part during the printing process), etc.
Material selection
1. Choose the appropriate plastic material according to the use and performance requirements of the part. Common materials include ABS, PLA etc., ABS has good strength and toughness, PLA is more environmentally friendly and easy to print.
2. Make sure the material you choose is compatible with your 3D printer, and understand the properties of materials, Such as melting point, Shrinkage, etc., In order to make corresponding parameter adjustments during the printing process.
Preparing for printing
1. Import the designed model file into the 3D printer software, Perform slicing. Slicing software will divide the model into several layers, And generate a command file that can be recognized by the printer.
2. Set printing parameters, including layer thickness, Printing speed, Temperature etc., Generally speaking, Smaller layer thickness improves printing accuracy, But it will increase the printing time; Proper printing speed and temperature can ensure good extrusion and bonding of materials.
Printing process
1. Check the status of your 3D printer, Make sure the nozzle, Platform and other components work normally. Load the selected plastic material into the printer’s feeding mechanism.
2. Start the printer, Start printing。During printing, Observe the operation of the printer, Pay attention to whether anything abnormal occurs, If material is clogged, Print offset, etc., if something goes wrong, Pause printing and process it in time.
Post-processing
1. After printing is completed, Carefully remove the part from the build platform. Remove support structures from parts, You can use tools such as scissors, pliers, etc.) for careful removal.
2. Post-process parts, such as polishing, Polishing etc., to improve surface quality. if needed, Can be colored, Coating and other treatments, Enhance part aesthetics and performance.
Whether you need a small number of parts or 10000 Multiple production objects that are ultimately put into use, CNC machining is an ideal manufacturing method. The following are the customized CNC services we launch.
By Rapidefficient, You can complete product manufacturing in a short time, so as to be able to quickly enter the market.
Efficient mold making is a cost-effective way, Able to bridge the gap between sample production and mass production. Quickly let your products occupy the market.
For custom projects, Our professional team will help you achieve the best products in terms of quality and efficiency.
All information and uploaded materials are secure and confidential.
The printed surface is rough
Performance: The surface of the printed plastic parts has obvious layers, not smooth enough.
reason: The printing layer is thicker, Printing speed is too fast, The nozzle temperature is unstable, etc.
Solution
Reduce print layer thickness, Improve printing accuracy.
Reduce printing speed, Give materials enough time to blend.
Adjust the nozzle temperature, Ensure stability within the appropriate range.
Post-process prints, such as polishing, Polishing etc.
The print is not strong enough
Performance: Plastic parts are prone to breakage or deformation, Poor ability to withstand external forces.
reason: Improper material selection, The printing parameters are unreasonable, Unreasonable part structure design, etc.
Solution
Choose stronger plastic materials.
Optimize printing parameters, If increasing filling density, Reduce printing speed, etc.
Improve part structure design, Add reinforcement and other structures.
Jam occurs during printing
Performance: The nozzle cannot extrude material normally, Causes printing to be interrupted.
reason: Material quality is poor, The nozzle temperature is too high or too low, Printing speed is too fast, etc.
Solution
Check material quality, Ensure no impurities.
Adjust the nozzle temperature, Adapt it to the properties of the material.
Reduce printing speed, Avoid material accumulation at the nozzle.
Clean nozzles regularly, Prevent clogging.
Print size deviation
Performance: The printed part size does not match the design size.
reason: Printer accuracy problem, Material shrinkage is large, Printing parameter setting errors, etc.
Solution
Calibrate printer accuracy, Make sure the print size is accurate.
Consider material shrinkage, Compensate for dimensions during design.
Check printing parameter settings, Make sure it’s correct.
Print warped
Performance: Parts deform during or after printing, edge lifted.
reason: Printing platform temperature is uneven, Material shrinkage is large, Printing speed is too fast, etc.
Solution
Ensure the printing platform temperature is even, Auxiliary equipment such as heated beds can be used.
Choose plastic materials with smaller shrinkage rates.
Reduce printing speed, Allow material enough time to cool and solidify.
Apply glue or other fixing methods to the build platform, Prevent parts from warping.
Our CNC machining services have been praised by global customers from different fields, We supply CNC machining components to a variety of industries,Covers the following and more.
Large size parts, Such as CNC machined ABS bumpers, PC/ABS instrument panels and precision automotive parts, Reflector for example, lens, Steering wheel assembly, engine, transmission.
Robot parts for the robotics and automation industry, actuator, end effector, Motor, Automatic control equipment, Fixtures and housings.
Stainless steel or titanium bone plate, prosthesis, respiratory equipment, handheld device, diagnostic equipment, anatomical model, Components for medical needs such as surgical instruments.
Aero engine, body, turbine, brake, tire parts, lighting system, Vacuum pump and fuel pump parts.
Consumer products, such as electronic equipment casings, button, handle, Knob, switch, wearable digital devices, Cookware products, sports equipment.
New energy industry components, e.g. heat exchanger, valve, pipeline, Pumps and accessories, Hydraulic components, Battery components, solar panel components, Frame and impeller.
Electronic housing, conveyor belt, fastener, connector, Generator components, fixtures, Machine and tool parts for industrial machinery.
Actual models can be created based on semiconductor requirements, Engineering models and other experimental equipment, We work with universities around the world.