Sheet metal processing
Serve
Sheet metal processing is a comprehensive processing technology for metal sheets, Mainly includes cutting metal sheets, stamping, bend, welding, Surface treatment and a series of operations, to make them into parts or products of various shapes and sizes.
One-off CNC machining prototype
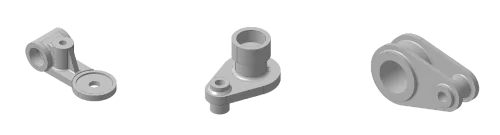



Our sheet metal processing capabilities
There are many reasons to choose Rapidefficient sheet metal processing. first, It has advanced equipment and technology, Able to complete sheet metal processing tasks efficiently and quickly, Greatly shorten the production cycle. Secondly, High-precision processing ensures stable and reliable product quality, Meets a variety of stringent size and shape requirements. Furthermore, Can flexibly cope with small batch and multi-variety production, Meet individual needs. at the same time, Pay attention to material utilization, Reduce costs. Professional team provides quality services, From design to finished product, Strict control throughout the process. select it, Just choose efficiency, Quality and reliability, Bring exceptional value to your project.
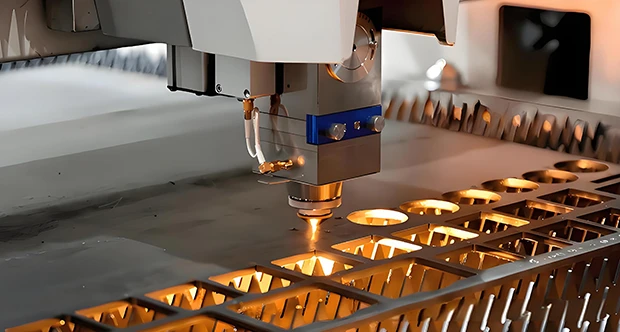
Sheet metal processing is a comprehensive processing technology for metal sheets, Mainly includes cutting metal sheets, stamping, bend, welding, Surface treatment and a series of operations, to make them into parts or products of various shapes and sizes. through these processes, Precise forming and functional customization of metal sheets can be achieved, Meet the diverse needs of different industries.
Commonly used sheet metal materials include stainless steel, carbon steel, Aluminum etc. Stainless steel is corrosion resistant, High temperature resistance, High strength and other characteristics, Widely used in medical equipment, food processing machinery, Chemical equipment and other fields. Carbon steel has good strength and toughness, The price is relatively low, Suitable for machinery manufacturing, Building structures and other fields. Aluminum material is light, Corrosion resistant, Good thermal conductivity, Commonly used in electronic equipment housings, Aerospace parts and other fields. When choosing sheet metal materials, Need to be based on the use environment of the product, Performance requirements, Comprehensive consideration of factors such as cost.
The main steps of sheet metal processing are as follows:
Cut: Use a shearing machine to cut the metal sheet according to the designed size, Get the desired sheet shape.
Stamping: Punching the plate with a punch, drop fee, Stretching and other operations, Form holes of various shapes, Grooves and Bosses.
Bending: Use a bending machine to bend the plate according to the designed angle, Create boxes of different shapes, Frame and other structures.
Welding: Use welding technology to join multiple sheet metal parts together, form a complete product. Common welding methods include argon arc welding, Carbon dioxide shielded welding, etc.
surface treatment: Surface treatment of sheet metal products, to improve its corrosion resistance, Aesthetics and wear resistance. Surface treatment methods include spraying, plating, Oxidation, etc.
Precision electronic equipment housing manufacturing
High-precision cutting and forming:
Ability to accurately laser cut sheet metal, CNC punch cutting and other operations, Ensure the dimensional accuracy of the housing reaches micron level, Meet the installation needs of various precision electronic components. For example,cell phone, Cases for tablets and other smart electronic devices, Its edges are neatly cut, Precise curvature at corners, Provides perfect accommodation space for internal electronic components.
Communication equipment cabinets and component processing
Cabinet structure design and processing:
According to the characteristics and installation requirements of communication equipment, Design and manufacture structurally sound, High strength cabinet. Made of high quality steel, Through precise blanking and welding processes, Ensure the overall stability and load-bearing capacity of the cabinet, Able to withstand the weight of a large amount of communication equipment and the test of long-term use.
Auto parts production
Car body structural parts processing:
Use large stamping equipment and molds, Manufacture various structural parts of automobile bodies, like car body beams, door frame, roof frame etc. Through precise stamping process, Ensure the dimensional accuracy and strength requirements of these structural parts, Provide guarantee for the overall safety and stability of the car.
Medical device shell and stent manufacturing
Sterile environment adaptable processing:
Use special metal materials that comply with medical device industry standards, Such as stainless steel 304L, 316L et al, Ensure that the processed housings and brackets have good corrosion resistance and biocompatibility, No use of drugs inside medical devices, Contamination caused by reagents, etc., It will not cause adverse effects on the patient’s body.
Aerospace parts manufacturing
High performance materials processing:
Processing of high-performance metal materials commonly used in the aerospace industry, Such as titanium alloy, Aluminum alloy, etc., These materials have high strength, High toughness and high temperature resistance. Through special processing technology and technology, such as thermoforming, Super plastic molding, etc., Ensure materials maintain their excellent properties during processing, Meet the use requirements of aerospace parts in extreme environments.
Smart device casing and frame manufacturing
Personalized design and rapid prototyping:
Able to meet customers’ individual needs, Design and manufacture smart device housings and frames with unique looks and structures. Leverage 3D modeling technology and rapid prototyping processes, Such as 3D printing, Laser sintering, etc., Produce samples quickly, For customers to evaluate and verify, Shorten product development cycle.
Parts display area in sheet metal processing, Various exquisite parts are eye-catching. Precision electronic equipment housing, Precise cutting, The bending angle is just right, Smooth and delicate surface treatment. Auto parts are strong and durable, Demonstrate superb stamping and welding skills. Communication equipment cabinet components have a rigorous structure, Ingenious ventilation and heat dissipation design. Medical device housings reflect stringent requirements for materials and precision. These parts fully demonstrate the diversity and exquisite craftsmanship of sheet metal processing, Provide reliable structural support for products in various industries.
1. High dimensional accuracy: Sheet metal processing uses advanced CNC equipment and precision molds, Able to achieve high-precision dimensional control. Whether it is cutting, Stamping or bending processes, Dimensional errors can be controlled within a very small range, Meet the needs of industries with high product accuracy requirements, Such as electronic, Medical equipment and other fields.
2. Complex shape processing: Through a combination of various processing techniques, Sheet metal processing can produce parts of various complex shapes. For example, Laser cutting can be used to cut any shape, Combined with bending, Stamping and other processes, Flat sheets can be processed into structural parts with three-dimensional shapes, Meet the design needs of different products.
1. Rich range of materials: Sheet metal processing can be applied to a variety of metal materials, such as stainless steel, carbon steel, Aluminum alloy, etc., Different materials have different performance characteristics, You can choose according to the use environment and functional requirements of the product. For example, Stainless steel is corrosion resistant, High temperature resistance properties, Suitable for chemical industry, Food processing and other industries; Aluminum alloy is lightweight, High strength, Suitable for aerospace, Automobile and other fields.
2. High strength: The metal sheet itself has high strength and stiffness, Parts processed by sheet metal can withstand large external forces and loads. Through reasonable structural design and processing technology, Can further improve the strength and stability of parts, Ensure product safety and reliability during use.
1. Efficient mass production: Sheet metal processing adopts mechanized and automated production methods, Enables efficient mass production. For example, CNC punch press, Equipment such as laser cutting can quickly process large numbers of parts, Greatly improved production efficiency. at the same time, The process flow of sheet metal processing is relatively simple, Easy to achieve standardization and large-scale production, Reduced production costs.
2. Cost effective: Compared with other processing methods, Sheet metal processing is highly cost-effective. on the one hand, The cost of sheet metal materials is relatively low, And it can be done through reasonable typesetting and cutting, Improve material utilization, Reduce waste. on the other hand, Sheet metal processing equipment and mold investment are relatively small, Maintenance costs are also lower, Suitable for small and medium-sized enterprises to produce.
Design stage
1. Clarify needs: Determine product functionality, size, shape, Materials and other requirements, As well as the use environment and special requirements (such as waterproof, dust-proof, Earthquake resistance, etc.).
2. Drawings: Create detailed 2D or 3D drawings using professional design software, Mark each size clearly, tolerance, Surface treatment requirements, etc.
3. Feasibility analysis: Communicate with sheet metal processing manufacturers or engineers, Evaluate design feasibility, including processing difficulty, cost, Production cycle, etc.
Material selection
1. Considerations: According to product performance requirements, cost budget, Choose appropriate sheet metal materials based on appearance requirements, etc., such as stainless steel, carbon steel, Aluminum alloy, etc.
2. Material properties: Understand the strength of different materials, hardness, Corrosion resistance, Processability and other properties, to make the best choice.
3. Material thickness: Based on product strength requirements and cost considerations, Choose the right material thickness.
Processing technology
1. Cutting: Using laser cutting, plasma cutting, Shears and other equipment cut the sheet into the required shape and size.
2. Stamping: Use punches and dies to punch various holes in the plate, groove, Boss and other shapes.
3. Bend: Use a bending machine to bend the sheet into the desired angle and shape, Pay attention to the precision control of bending radius and angle.
4. Welding: Using argon arc welding, carbon dioxide shielded welding, Welding methods such as spot welding join multiple sheet metal parts together.
5. Surface treatment: According to product appearance requirements and usage environment, Choose the right surface treatment method, Such as spraying, plating, Oxidation, etc.
Quality control
1. Dimensional accuracy: Use measuring tools (such as calipers, micrometer, Three-dimensional coordinate measuring instrument, etc.) to measure the dimensions of processed parts, Ensure dimensions meet design requirements.
2. Appearance quality: Check the surface of the part for scratches, Dimple, Deformation and other defects, Is the surface treatment uniform, beautiful.
3. Welding quality: Check whether the welding joint is firm, No pores, Defects such as slag inclusions, Is the weld smooth, beautiful.
4. Assembly test: Assembly and testing of processed parts, Check whether the assembly is smooth, Is there interference, Problems such as looseness.
Packaging and shipping
1. Packaging: According to the shape of the part, Dimensions and weight, Choose the right packaging method, like wooden box, carton, Foam plastics, etc., Ensure parts are not damaged during transportation.
2. Logo annotation: Clearly mark the product name on the packaging, Specification, quantity, Production date and other information, Easy to identify and manage.
3. Transportation method: Choose the right shipping method, Such as express delivery, logistics, Private car, etc., Ensure parts arrive at their destination on time.
Whether you need a small number of parts or 10000 Multiple production objects that are ultimately put into use, CNC machining is an ideal manufacturing method. The following are the customized CNC services we launch.
By Rapidefficient, You can complete product manufacturing in a short time, so as to be able to quickly enter the market.
Efficient mold making is a cost-effective way, Able to bridge the gap between sample production and mass production. Quickly let your products occupy the market.
For custom projects, Our professional team will help you achieve the best products in terms of quality and efficiency.
All information and uploaded materials are secure and confidential
Dimensional deviation
Performance: The size of the processed sheet metal parts does not match the design size, May be too big or too small.
Reason: Equipment accuracy is not enough, Mold wear, Material deformation, Programming errors, etc.
Surface quality issues
Performance: There are scratches on the surface, Dimple, bulge, Oxidation, Rust, etc.
Reason: Material quality issues, Improper operation during processing, Equipment failure, etc.
Deformation problem
Performance: Sheet metal parts are deformed during or after processing, Affect product quality.
Reason: Material internal stress, Unreasonable processing technology, Improper welding, etc.
Glitch problem
Performance: There are burrs on the edges of sheet metal parts, not smooth.
Reason: Cutting tool wear, Improper setting of cutting parameters, etc.
Welding problem
Performance: There are pores in the welding joint, Slag inclusion, Defects such as cracks, Welding strength is not enough.
Reason: Improper setting of welding process parameters, Inappropriate selection of welding materials, The technical level of the operators is not enough, etc.
Material diversity and quality control
1. Differences in properties of different materials: Sheet metal processing may involve a variety of metal materials, such as stainless steel, carbon steel, Aluminum alloy, etc., Each material has different mechanical properties, Processing characteristics and surface treatment requirements. For example, Stainless steel has good corrosion resistance, But the hardness is higher, Processing is difficult; Aluminum alloy is lightweight, But the intensity is relatively low, Special processing technology is required to ensure its structural strength. This requires processors to be familiar with the characteristics of various materials, In order to choose appropriate processing methods and parameters.
2. Material quality fluctuations: The quality of raw materials may fluctuate, If the thickness of the board is uneven, There are scratches or rust on the surface, etc., These quality issues may affect processing accuracy and product quality. therefore, Raw materials need to be strictly inspected and screened before processing, To ensure that material quality meets requirements. at the same time, It is also necessary to establish good cooperative relationships with suppliers, Ensure stable supply of raw materials and controllable quality.
High precision requirements and processing error control
1. Dimensional accuracy challenge: Many sheet metal products require high dimensional accuracy, Especially in electronics, communication, Medical and other fields. For example, The dimensional accuracy of electronic equipment enclosures directly affects the installation and performance of internal components; Sheet metal components for medical devices require strict dimensional control, To ensure the safety and reliability of equipment. However, In the actual processing process, Due to equipment accuracy, Mold wear, Influence of factors such as material deformation, It is difficult to guarantee complete dimensional accuracy. This requires the use of high-precision processing equipment and detection methods, And strict quality control system to ensure the dimensional accuracy of products.
2. Shape accuracy conundrum: In addition to dimensional accuracy, The shape accuracy of sheet metal products is also very important. complex bends, Stamping and welding processes may cause shape deviations, Affect the appearance and assembly performance of the product. For example, The bending angle is inaccurate, The outline of the stamping parts is not clear, Problems such as welding deformation may affect the quality of the product. In order to solve these problems, Need to optimize processing technology, Improve mold accuracy, Adopt reasonable welding sequence and control welding parameters and other measures.
Complex shape and process design
1. Complex shape processing difficulty: With the continuous innovation of product design, The shapes of sheet metal products are becoming more and more complex, Brings great challenges to processing. For example, Has a curved surface, Special-shaped hole, Sheet metal parts with complex shapes such as thin-walled structures, Special processing techniques and equipment are required to achieve this. This requires processors to have rich experience and innovative capabilities, Ability to design reasonable processing techniques and molds based on product shape characteristics.
2. Process design complexity: Sheet metal processing involves multiple process links, such as cutting, stamping, bend, welding, Surface treatment, etc., Each process step has its own unique requirements and challenges, Reasonable process design and optimization are required. For example, in the cutting process, It is necessary to choose the appropriate cutting method and parameters, To ensure cutting quality and efficiency; In the stamping process, Reasonable design of mold structure and stamping sequence is required, to avoid cracks, Defects such as wrinkles; in welding process, It is necessary to choose the appropriate welding method and parameters, To ensure welding strength and appearance quality. at the same time, It is also necessary to consider the connection and cooperation between various process links, To ensure the smooth progress of the entire processing process.
Cost control and efficiency improvement
1. cost pressure: Competition in the sheet metal processing industry is fierce, Customers are price sensitive, This has brought great cost pressure to enterprises. Raw material cost, Equipment investment, Labor cost, Energy consumption and other factors are important factors affecting costs. in order to reduce costs, Enterprises need to optimize production processes, Improve material utilization, Reduce equipment failure rate, Improve production efficiency, etc. at the same time, Effective cost negotiations with suppliers are also required, Get a better purchase price.
2. Efficiency improvement problem: Improving production efficiency is the key for enterprises to gain advantages in market competition. However, There are many factors that affect efficiency in the sheet metal processing process, If equipment debugging takes a long time, Complex process, Production batch is small etc., in order to improve efficiency, Enterprises need to adopt advanced processing equipment and automation technology, Optimize production process, Reduce non-productive time. at the same time, Production management also needs to be strengthened, Improve employee productivity and skill levels.
Our CNC machining services have been praised by global customers from different fields。We supply CNC machining components to a variety of industries,Covers the following and more
Large size parts, Such as CNC machined ABS bumpers, PC/ABS instrument panels and precision automotive parts, Reflector for example, lens, Steering wheel assembly, engine, transmission.
Robot parts for the robotics and automation industry, actuator, end effector, Motor, Automatic control equipment, Fixtures and housings.
Stainless steel or titanium bone plate, prosthesis, respiratory equipment, handheld device, diagnostic equipment, anatomical model, Components for medical needs such as surgical instruments.
Aero engine, body, turbine, brake, tire parts, lighting system, Vacuum pump and fuel pump parts.
Consumer products, such as electronic equipment casings, button, handle, Knob, switch, wearable digital devices, Cookware products, sports equipment.
New energy industry components, e.g. heat exchanger, valve, pipeline, Pumps and accessories, Hydraulic components, Battery components, solar panel components, Frame and impeller.
Electronic housing, conveyor belt, fastener, connector, Generator components, fixtures, Machine and tool parts for industrial machinery.
Actual models can be created based on semiconductor requirements, Engineering models and other experimental equipment, We work with universities around the world.