Stainless steel is widely used in CNC machining due to its excellent corrosion resistance, high strength and temperature resistance. Different stainless steel types are suitable for different application scenarios, each with its own advantages and disadvantages. This article will introduce in detail the performance of several common stainless steel types in CNC machining and conduct a comparative analysis.
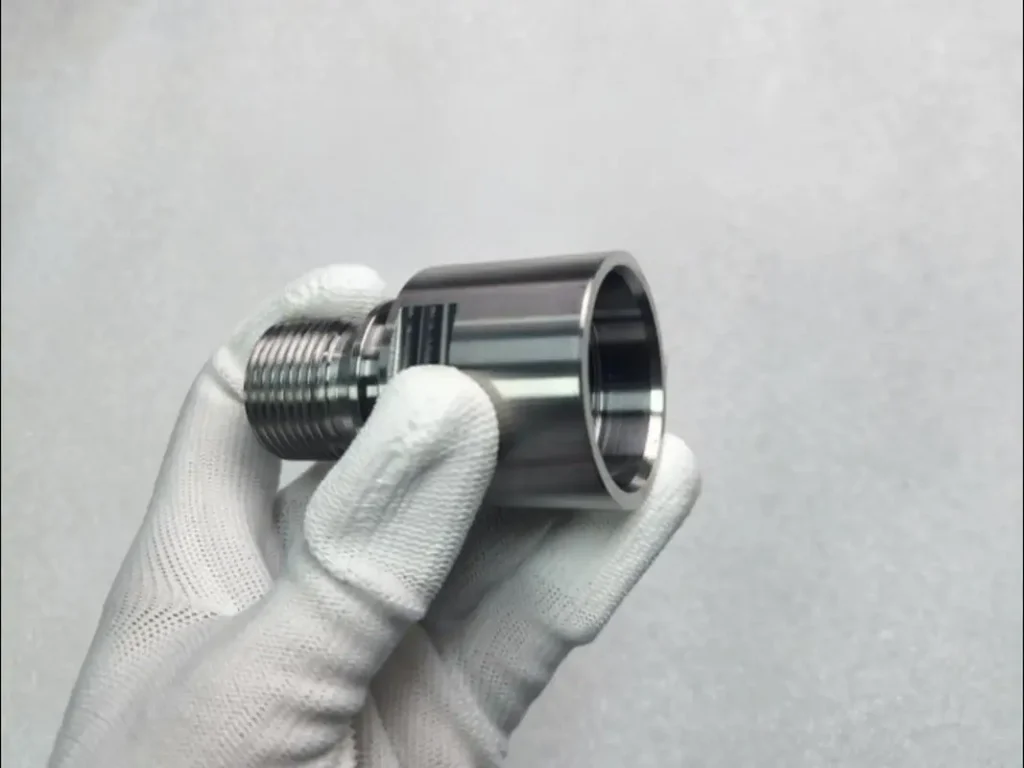
1. 304 stainless steel cnc machining parts
Advantages:
Wide applicability: 304 stainless steel is one of the most commonly used stainless steels and is suitable for a variety of industrial and household applications.
Good corrosion resistance: Contains 18% to 20% chromium and 8% to 10% nickel, providing excellent corrosion resistance.
Processability: Can be processed into complex shapes by CNC, and has good welding performance.
No heat treatment hardening phenomenon: Easy to process and manufacture.
Disadvantages:
Higher cost: Due to the high proportion of nickel, the cost is relatively high.
Moderate strength: Although the strength is good, it is not as good as some high-strength stainless steel models.
2. 316 stainless steel cnc machining parts
Advantages:
Higher corrosion resistance: Compared with 304 stainless steel, 316 stainless steel adds molybdenum to improve corrosion resistance to reducing media.
Suitable for harsh environments: Suitable for use in seawater and other chemical media, commonly used in marine and chemical industries.
Disadvantages:
Higher cost: Due to the addition of molybdenum, the cost is higher than 304 stainless steel.
Slightly more difficult to process: Requires harder cutting tools and more precise processing techniques.
3. 201 stainless steel parts CNC processing
Advantages:
Lower cost: Compared with 304 stainless steel, 201 stainless steel contains a lower nickel content, so it is less expensive.
Good formability: Suitable for applications that require deep drawing and other forming processes.
Disadvantages:
Poor corrosion resistance: Due to the lower nickel content, the corrosion resistance is not as good as 304 and 316 stainless steel.
Easy to rust: More likely to rust in humid or corrosive environments.
4. 430 stainless steel parts CNC processing
Advantages:
Cost-effectiveness: Due to the absence of nickel, the cost of 430 stainless steel is relatively low.
Magnetic properties: It is magnetic and suitable for applications that require magnetism.
Disadvantages:
Limited corrosion resistance: Compared with 300 series stainless steel, the corrosion resistance is lower.
Low strength: The strength and hardness are relatively low, not suitable for high-strength applications.
Precautions for stainless steel CNC machining
Choose the right stainless steel grade: Different stainless steel grades have different compositions, properties and uses. You need to choose the right stainless steel grade according to the function, environment, load and other factors of the part.
Choose the right cutting parameters: Cutting parameters include cutting speed, feed speed, cutting depth, back cutting amount, etc., which affect the surface quality, dimensional accuracy, cutting force, thermal deformation, etc. of the part.
Choose the right tool material: The tool material determines the wear resistance, heat resistance, toughness, etc. of the tool, which affects the surface quality, dimensional accuracy, cutting force, etc. of the part.
Choose the right surface treatment: Surface treatment includes polishing, sandblasting, spraying, electroplating and other methods, which can improve the appearance, protective performance, friction coefficient, etc. of the part.
When choosing stainless steel CNC machining, you need to decide the most suitable stainless steel model according to the specific application requirements, cost budget and processing difficulty. For example, for applications that require high corrosion resistance, 316 stainless steel may be the best choice; while for cost-sensitive applications with low corrosion resistance requirements, 201 or 430 stainless steel may be more suitable. Understanding the characteristics and limitations of each stainless steel can help manufacturers select the most appropriate material to achieve the best processing results and cost-effectiveness.