I. Introduction to Wire-cut Machining
A. Definition and Basic Principle
Wire-cut machining, also known as Wire Electrical Discharge Machining (WEDM), is a remarkable electro-machining technique. In this process, a continuous moving thin metal wire, often made of materials like molybdenum, tungsten or copper, serves as the electrode. The basic working principle involves pulsed spark discharge. When the electrode wire, which is connected to the cathode of a pulse power supply, gets close enough to the workpiece (connected to the anode) with an appropriate gap filled with working fluid having certain insulating properties, the pulse voltage will cause the working fluid to break down. This breakdown forms an instantaneous discharge path between the wire and the workpiece.
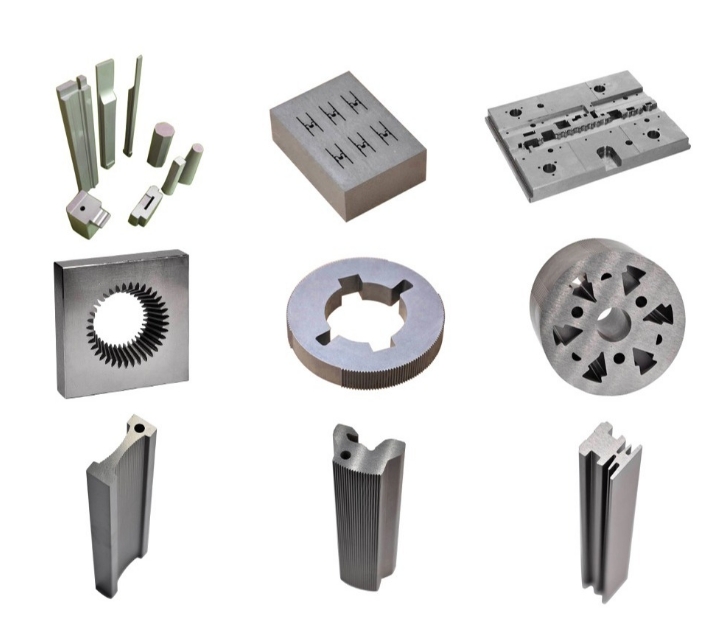
The discharge generates an extremely high temperature, reaching around 10,000℃ to 12,000℃ in an instant. Such a high temperature makes the metal of the workpiece melt and even vaporize at the discharge point. Meanwhile, the working fluid between the wire and the workpiece vaporizes and expands rapidly, creating a shock wave similar to an explosion that throws out the melted and vaporized metal from the discharge location. Through continuous pulsed power supply and repeated discharges, the material of the workpiece is continuously removed. Coupled with the relative movement of the workpiece table with respect to the electrode wire as per the preset requirements, specific shapes of workpieces can be machined precisely.
B. Types of Wire-cut Machining
- High-speed Wire-cut Machining
The wire movement speed in high-speed wire-cut machining is relatively fast, usually within the range of 6 to 12 m/s. In this type, the electrode wire makes a high-speed reciprocating motion. It is a commonly used method in many manufacturing scenarios where the requirement for machining efficiency is relatively high while the tolerance for the roughness of the cutting surface is a bit looser. For example, in some simple mold production or the processing of parts that don’t demand extremely high precision, high-speed wire-cut can complete the cutting task quickly. However, due to the high-speed reciprocating movement of the wire, it may cause relatively larger vibrations and is more likely to break the wire compared to other types. Also, the cutting accuracy is generally not as high as that of low-speed wire-cut machining.
- Medium-speed Wire-cut Machining
Medium-speed wire-cut machining is a relatively new process developed in recent years based on high-speed wire-cut machining. It realizes the function of variable frequency and multiple cutting on the basis of high-speed wire-cut. By adjusting the cutting parameters and the number of cutting passes during the process, it can improve the cutting accuracy and surface quality to a certain extent compared to traditional high-speed wire-cut. It strikes a balance between machining efficiency and precision, making it suitable for some parts that require better quality on the cutting surface while still needing to maintain a certain level of production speed.
- Low-speed Wire-cut Machining
In low-speed wire-cut machining, the wire moves at a much slower speed, typically around 0.2 m/s, and it makes a low-speed unidirectional movement. This kind of wire-cutting is mainly used in situations where high cutting precision and a smooth cutting surface are required. For instance, in the manufacturing of high-precision molds, aerospace components, and some key parts in the electronics industry, low-speed wire-cut can achieve excellent results. Since the wire is used only once in the unidirectional movement and usually equipped with automatic wire threading and constant tension devices, it can ensure stable machining with less wire vibration and higher accuracy. However, it also has limitations such as being less suitable for processing workpieces with large thicknesses and having relatively higher equipment and operating costs.
II. Advantages of Wire-cut Machining
A. High Precision Cutting
Wire-cut machining is renowned for its remarkable high precision cutting capabilities. It can achieve accuracy levels that are often difficult for many other cutting technologies to match. For instance, when machining intricate parts for the electronics industry like microchips’ lead frames or the tiny components in smartphones, wire-cut machining can maintain tolerances within a few microns.
Take the manufacturing of high-precision molds as another example. In creating the cavities and cores of molds that require extremely precise dimensions to ensure the final products’ quality, wire-cut machining plays a vital role. It can precisely cut complex shapes with minimal errors in size and geometry. Compared to traditional cutting methods such as mechanical milling or turning, wire-cut machining doesn’t generate significant cutting forces that might cause deformations to the workpiece. This characteristic allows it to handle delicate materials and thin-walled structures with ease while still maintaining the desired precision. Whether it’s processing materials like hardened steel, titanium alloys, or even some brittle materials like ceramics in certain applications, wire-cut machining can consistently deliver accurate and high-quality cuts, making it the top choice for many industries where precision is of utmost importance.
B. Ability to Handle Complex Shapes
One of the outstanding features of wire-cut machining is its ability to process workpieces with complex and delicate shapes that pose challenges for other machining methods. In the production of intricate molds, for example, molds with complex internal cavities, undercuts, or fine details can be precisely machined using wire-cut technology. The thin wire electrode can access narrow spaces and create shapes that are otherwise impossible to achieve with traditional cutting tools like end mills or lathe tools.
Moreover, in the field of microstructures manufacturing, wire-cut machining shines. It can fabricate micro-components with features on a micrometer scale, such as micro-gears, micro-sensors, and micro-fluidic channels. These tiny structures are essential in various high-tech industries like biomedical engineering and microelectromechanical systems (MEMS). Unlike other machining techniques that might struggle to reach into small areas or accurately shape such delicate geometries, wire-cut machining can follow the programmed paths precisely to bring these complex and minuscule shapes to life. This unique capability enables designers and engineers to push the boundaries of innovation and create products with more advanced functions and better performance by taking advantage of the complex shapes that wire-cut machining can handle.
C. Cost-effective in Certain Scenarios
Wire-cut machining can prove to be highly cost-effective in several specific situations. Firstly, in terms of the production cycle, when dealing with small to medium batch production of parts with complex shapes, wire-cut machining can often complete the job faster than traditional machining methods that might require multiple setups and tool changes. For example, in the production of custom-made jewelry pieces or specialized mechanical parts with unique geometries, wire-cutting can reduce the overall production time by eliminating the need for elaborate fixturing and complex tooling arrangements.
Considering the manufacturing cost, although the initial investment in wire-cut machining equipment might be relatively high, in the long run, for certain materials and part requirements, it can save costs. For instance, when working with hardened materials that are difficult to machine using conventional cutting tools and would require frequent tool replacements, wire-cut machining, which relies on electrical discharge rather than physical cutting forces, can avoid these additional tooling costs.
In terms of material utilization, wire-cut machining is also advantageous. It has a relatively narrow kerf width compared to some other cutting processes, which means less material is wasted during the cutting operation. In applications where the raw material is expensive or in short supply, this efficient use of material can significantly contribute to cost savings. For example, in the aerospace industry when machining high-value titanium alloy components, the ability of wire-cut machining to minimize material waste while achieving the required precision makes it a cost-effective choice over alternative cutting techniques that might result in more material being discarded during the machining process.
III. Rapidefficient in CNC Machining Market
A. Rapidefficient’s Definition and Significance
In the realm of CNC machining, “rapidefficient” refers to the ability to carry out machining tasks with both speed and high efficiency while maintaining excellent quality. It means optimizing every aspect of the machining process, from the movement of the cutting tools to the overall workflow, to ensure that workpieces are produced in a shorter time frame without sacrificing precision.
Rapidefficient is of great significance as it directly impacts the productivity and competitiveness of manufacturing enterprises. In today’s fast-paced manufacturing world, where time is money and quality is non-negotiable, being able to machine parts rapidly and efficiently allows companies to meet tight deadlines, reduce production costs, and respond quickly to market demands. For example, in the automotive industry, rapidefficient CNC machining enables the quick production of engine components and body parts, ensuring a smooth supply chain and timely delivery of vehicles to the market. In the aerospace sector, it helps in fabricating intricate and high-precision parts like turbine blades and fuselage components in a timely manner, which is crucial for the progress of projects.
B. How Rapidefficient Enhances Wire-cut Machining
Rapidefficient features play a vital role in enhancing wire-cut machining in several ways. Firstly, it can significantly reduce the processing time. Through optimized wire movement speeds and precise control of the electrical discharge pulses, the cutting process becomes faster. For instance, in high-speed wire-cut machining, by adjusting the parameters based on the rapidefficient concept, the wire can make more efficient reciprocating motions, cutting through workpieces quicker than traditional setups.
Secondly, it enhances cutting accuracy. Advanced algorithms and control systems in rapidefficient CNC machines ensure that the wire electrode follows the programmed cutting paths with minimal deviations. This is especially important in wire-cut machining where precision is key, such as when manufacturing microelectronic components or high-precision molds. The ability to maintain a consistent gap between the wire and the workpiece and precisely control the discharge energy contributes to accurate cuts.
Moreover, rapidefficient improves the overall productivity. It allows for continuous operation with fewer interruptions due to wire breakages or other issues. Automatic wire threading systems in rapidefficient wire-cut machines can quickly replace the wire when needed, minimizing downtime. Additionally, by integrating with smart manufacturing systems, it enables better management of multiple machining tasks simultaneously, optimizing the use of resources and increasing the number of workpieces produced in a given time period.
C. Success Stories or Case Studies
One real-world example of rapidefficient in wire-cut machining is a precision mold manufacturing company. They were facing challenges in meeting the tight delivery schedules for complex molds required by their clients in the consumer electronics industry. By implementing rapidefficient CNC wire-cut machines, they were able to reduce the processing time of each mold by nearly 30%. The optimized wire movement and precise control of the cutting process ensured that the intricate internal cavities and fine details of the molds were machined with high accuracy. As a result, they not only met the delivery deadlines but also improved the quality of their molds, leading to fewer rejects and higher customer satisfaction.
Another case is in the aerospace component manufacturing field. A company was tasked with producing a large number of turbine blade prototypes for a new engine design. Using rapidefficient wire-cut machining technology, they managed to increase the productivity by 40%. The enhanced cutting accuracy allowed them to create the complex geometries of the turbine blades precisely, meeting the strict aerodynamic and structural requirements. The reduced processing time also enabled them to conduct more iterations and tests in a shorter period, accelerating the overall development process of the new engine.
These examples clearly demonstrate the practical value of rapidefficient in wire-cut machining projects, highlighting its ability to transform manufacturing processes and drive success in various industries.
IV. Comparison with Other Cutting Technologies
A. Laser Cutting
Wire-cut machining and laser cutting are two distinct cutting technologies, each with its own characteristics in multiple aspects.
- Cutting range: In terms of materials, laser cutting has a broader application range as it can handle both metal and non-metal materials like fabrics and plastics. For example, it can precisely cut leather for making high-quality bags or cut through thin metal sheets for electronic enclosures. However, wire-cut machining is mainly applicable to conductive materials. When it comes to thickness, laser cutting is typically used for relatively thinner materials. For instance, in industrial applications for carbon steel, it’s usually for thicknesses below 20mm and for stainless steel, generally below 16mm. As the thickness increases, the cutting speed of laser cutting drops significantly. In contrast, wire-cut machining can handle thicker workpieces, with a general thickness range of 40 – 60mm and can even reach up to 600mm in some cases.
- Cutting speed: Laser cutting is known for its high speed. For example, when cutting a 2mm thick low-carbon steel plate with a 1200W laser, the cutting speed can reach 600cm/min. On the other hand, wire-cut machining is relatively slower, with an efficiency usually ranging from 20 to 60 square millimeters per minute and a maximum of around 300 square millimeters per minute.
- Precision: Laser cutting can achieve a size accuracy of about ±0.2mm with a narrow cut width of around 0.5mm. Wire-cut machining, especially in low-speed wire-cut, can reach a much higher precision with an accuracy level generally within ±0.01 – ±0.02mm and a minimum cut width of about 0.1 – 0.2mm.
- Surface quality: The surface roughness of laser-cut workpieces may not be as good as that of water-cut ones, especially for thicker materials, as it belongs to a thermal cutting method that can change the texture around the cutting area. Wire-cut machining can provide a relatively smooth surface for conductive materials within its precision range.
- Cost: Laser cutting equipment has a high investment cost, especially for high-power and high-precision models. For example, a 1000W fiber laser cutting machine can cost over a million dollars. Although it has no consumables like wire in wire-cut machining, its maintenance and operation costs are also relatively high. Wire-cut machining equipment is generally less expensive, usually in the range of several tens of thousands of dollars, but it requires consumables such as molybdenum wire or copper wire and cutting coolant.
In summary, wire-cut machining has unique advantages in processing thick conductive materials with high precision, while laser cutting shines in quickly cutting a wide variety of materials, especially thin ones, with relatively good precision.
B. Plasma Cutting
The differences between wire-cut machining and plasma cutting are significant in several key aspects.
- Cutting principles: Plasma cutting relies on the heat generated by a high-temperature plasma arc to melt and evaporate the metal at the workpiece’s cutting point and then uses the momentum of the high-speed plasma to expel the molten metal to form a cut. Wire-cut machining, on the other hand, uses pulsed spark discharge between the electrode wire and the workpiece in an insulating working fluid to melt and vaporize the workpiece material for cutting.
- Applicable materials: Plasma cutting is mainly used for cutting various metal materials such as stainless steel, aluminum, copper, cast iron, and carbon steel. Wire-cut machining is limited to conductive materials. For instance, plasma cutting is a good choice for processing large metal plates in the construction industry. However, wire-cut machining is more favored in the manufacturing of precise conductive parts like those in the electronics or mold industries.
- Accuracy: Plasma cutting has relatively lower accuracy, usually within about 1mm. Wire-cut machining can achieve much higher precision, especially in low-speed wire-cut scenarios, with an accuracy that can reach up to ±0.004mm.
- Heat effect: Plasma cutting has a significant heat effect during the cutting process, which can cause thermal deformation of the workpiece and make it difficult to conduct secondary processing on the cutting surface. Wire-cut machining has less heat impact on the workpiece as the heat is mainly concentrated at the discharge point and dissipated quickly with the working fluid, resulting in better surface quality and less deformation for precise parts.
- Suitability for different production requirements: Plasma cutting is more suitable for cutting thick metal plates with relatively low precision requirements and where speed is more important in some industrial applications. For example, in cutting thick steel plates for shipbuilding. Wire-cut machining is ideal for manufacturing high-precision parts with complex shapes, like micro-components in the electronics industry or intricate molds.
In conclusion, depending on the specific production needs, whether it’s high precision or the ability to handle thick metal plates, one can choose between wire-cut machining and plasma cutting accordingly.
C. Water Cutting
When comparing wire-cut machining with water cutting, several aspects come into play.
- Cutting mechanism: Water cutting, also known as water jet cutting, uses high-pressure water jets (with or without abrasive particles added) to erode the material and create a cut. It is a cold cutting method that doesn’t rely on heat to remove material. In contrast, wire-cut machining uses electrical discharge energy to melt and vaporize the workpiece material for cutting.
- Impact on materials: Water cutting has minimal impact on the material’s properties around the cutting area as it doesn’t generate heat, making it suitable for materials that are sensitive to heat or have strict requirements on the integrity of the surrounding area. Wire-cut machining may have a certain impact on the surface layer of the workpiece due to the heat generated during the electrical discharge process, although it can still achieve high precision for conductive materials.
- Cutting efficiency: Water cutting can be relatively slow, especially when compared to laser cutting or some other high-speed cutting methods. It is not very suitable for large-scale batch production. Wire-cut machining also has a relatively low cutting speed compared to some thermal cutting methods but can offer high precision in processing conductive workpieces.
- Environmental factors: Water cutting requires a large amount of water and may generate wastewater if abrasive particles are used, which needs proper treatment to meet environmental protection requirements. Wire-cut machining uses working fluid that also needs to be managed and recycled properly to avoid environmental pollution.
Overall, water cutting is advantageous in cutting materials that require cold cutting and maintaining the original properties of the workpiece. Wire-cut machining stands out in precisely cutting conductive materials with complex shapes and high precision requirements, and both play important roles in different manufacturing scenarios based on their respective characteristics.
VI. Recommendation of Rapidefficient CNC Aluminum Processing Service Providers
B. Reasons for Recommendation
These service providers are recommended for several reasons. Firstly, they all have an excellent reputation in the industry. Over the years, they have completed numerous projects for different clients, and the quality of their processed aluminum parts has been widely recognized. For example, they have supplied high-quality aluminum components to well-known enterprises in the electronics, automotive and other industries, winning the trust of customers with stable product quality and on-time delivery.
Secondly, their equipment is advanced. As mentioned before, they are equipped with high-precision CNC machining centers, lathes and other machinery. These advanced equipment not only ensure the processing accuracy but also can improve the production efficiency. For instance, the high-power and high-speed spindles on some of the machines can handle aluminum materials quickly and precisely, realizing rapidefficient processing.
Moreover, their professional technical teams play a crucial role. The technicians in these companies have in-depth knowledge of CNC aluminum processing technology. They can accurately program the machining paths according to the design drawings of the parts, optimize the processing parameters to make full use of the advantages of the equipment, and quickly solve various problems encountered during the processing, ensuring the smooth progress of the production process.
In addition, good customer feedback also attests to their excellence. Many clients have given positive reviews about their services, praising their communication efficiency, flexibility in dealing with special requirements, and the ability to provide comprehensive after-sales service, which makes the cooperation process pleasant and reliable.
In conclusion, wire-cut machining is a remarkable precision cutting technology with unique features and significant advantages. It operates based on the principle of pulsed spark discharge, utilizing an electrode wire to remove material from conductive workpieces precisely. There are different types including high-speed, medium-speed, and low-speed wire-cut machining, each catering to specific production requirements in terms of efficiency and precision.
The advantages of wire-cut machining are plentiful. It offers high precision cutting that can achieve extremely tight tolerances, making it ideal for manufacturing intricate parts in industries like electronics and aerospace. Its ability to handle complex shapes enables the creation of molds and micro-components with elaborate geometries that other cutting methods might struggle with. Moreover, in certain scenarios, it proves to be cost-effective by reducing production time, saving on tooling costs for hard materials, and minimizing material waste.
Rapidefficient plays a crucial role in wire-cut machining within the CNC machining market. It not only reduces processing time but also enhances cutting accuracy and improves overall productivity. The real-world case studies we’ve seen demonstrate how implementing rapidefficient in wire-cut machining can lead to meeting tight deadlines, improving product quality, and driving success in various manufacturing projects.