I. Introduction
Automotive fasteners might seem like small and insignificant components, but they play a crucial role in the overall performance and safety of vehicles. These tiny parts are responsible for holding together various parts of a car, ensuring its structural integrity and functionality. From the engine to the body panels, every aspect of a vehicle relies on the proper selection and installation of fasteners. In this article, we will explore 11 different types of automotive fasteners, their unique features, and their applications.
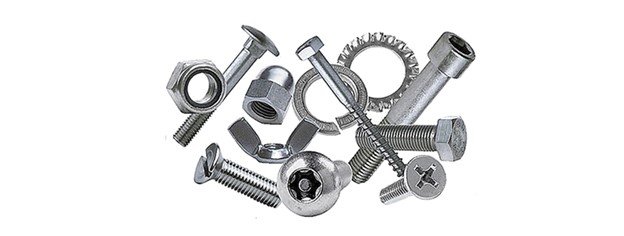
II. The Importance of Automotive Fasteners
Automotive fasteners are essential for the safety and performance of vehicles. They are used to hold together various parts of a car, such as the engine, transmission, chassis, and body panels. Without proper fasteners, these parts could come loose or separate, leading to serious accidents.
One of the most critical aspects of automotive fasteners is their ability to withstand the forces and vibrations that occur during driving. A loose or broken fastener can cause parts to rattle, which not only creates annoying noise but can also lead to premature wear and tear. In some cases, a failed fastener can even result in the detachment of a critical component, such as a wheel or a brake caliper, endangering the lives of the driver and passengers.
For example, if the bolts that hold the wheel to the axle are not tightened properly, the wheel could come off while the vehicle is in motion. This has happened in some cases where the torque specifications for the bolts were not followed during installation. Similarly, if the fasteners that secure the engine to the chassis are not strong enough or become loose over time, the engine could shift, affecting its performance and potentially causing damage to other components.
In addition to safety, automotive fasteners also play a significant role in the overall performance of a vehicle. They contribute to the structural integrity of the car, ensuring that it can handle the stresses and strains of normal driving conditions. Properly installed fasteners help to maintain the alignment of various parts, which is crucial for optimal handling and ride quality.
Moreover, the choice of fasteners can impact factors such as fuel efficiency and emissions. For instance, lightweight fasteners made from materials like aluminum or titanium can reduce the overall weight of the vehicle, leading to improved fuel economy. On the other hand, using incorrect or low-quality fasteners can increase the risk of leaks in the fuel or exhaust systems, which can have a negative impact on both performance and the environment.
Overall, automotive fasteners are not to be overlooked. They are the unsung heroes that keep our vehicles running smoothly and safely. In the following sections, we will explore the different types of automotive fasteners and their specific applications.
III. Different Types of Automotive Fasteners
1. Bolts
Bolts are one of the most commonly used automotive fasteners. They typically have a threaded shaft and a head, and are used in conjunction with nuts to hold parts together. Bolts come in various sizes, lengths, and strengths to suit different applications. For example, high-strength bolts are used in critical areas such as the engine and chassis to withstand heavy loads and vibrations. Hex bolts are widely used due to their easy installation and removal with a wrench. Some bolts also have special features, such as flange bolts that provide a larger bearing surface for better stability.
2. Nuts
Nuts are used to fasten bolts and keep them in place. They come in different shapes and sizes, including hex nuts, square nuts, and lock nuts. Lock nuts are designed to prevent loosening, which is crucial in automotive applications where vibrations can cause fasteners to come loose. There are various types of lock nuts, such as nylon insert lock nuts, which use a nylon ring to create friction and resist loosening, and prevailing torque nuts, which have a deformed thread or a special coating to provide a locking effect.
3. Screws
Screws are similar to bolts but are often used to attach components to thinner materials or in situations where a nut is not required. They have a threaded shaft and a head, and can be driven into place using a screwdriver or power tool. Wood screws are used for attaching interior trim and other wooden components in a car. Sheet metal screws are designed to cut through and grip thin metal sheets, making them suitable for attaching body panels and brackets. Self-tapping screws are particularly useful as they can create their own threads in pre-drilled or punched holes, saving time and effort during assembly.
4. Rivets
Rivets are permanent fasteners that are used to join two or more pieces of material together. They consist of a cylindrical shaft with a head on one end. To install a rivet, the shaft is inserted through holes in the materials to be joined, and the other end is then deformed to create a second head, clamping the materials together. Rivets are commonly used in the automotive industry for attaching body panels, as they provide a strong and reliable connection. There are different types of rivets, such as solid rivets, which are the most basic type, and blind rivets, which can be installed from one side and are often used in situations where access to the back of the joint is limited.
5. Washers
Washers are thin, flat discs that are used in conjunction with bolts and nuts. They serve several purposes, including distributing the load evenly, preventing damage to the surface of the materials being fastened, and providing a locking effect in some cases. Flat washers are the most common type and are used to increase the bearing surface area and protect the material from the sharp edges of the bolt or nut. Spring washers, on the other hand, are designed to provide a spring-like tension, which helps to prevent loosening due to vibrations. Lock washers, such as split lock washers, have a split in the ring that allows them to bite into the surface of the nut or bolt, providing additional resistance to loosening.
6. Retaining Rings
Retaining rings, also known as snap rings or circlips, are used to hold components in place on a shaft or in a groove. They are typically made of spring steel and have a circular shape with a gap. Retaining rings are easy to install and remove, and are often used in applications where a more permanent fastening method is not required or practical. For example, they are used to hold bearings, gears, and other rotating parts in place on a shaft, preventing them from moving axially. There are different types of retaining rings, including internal retaining rings, which are installed in a groove on the inside of a bore, and external retaining rings, which are installed on the outside of a shaft.
7. Snap Rings
Snap rings are similar to retaining rings and are used to provide a retaining force. They are usually made of spring steel and have a C-shaped or circular design. Snap rings are commonly used in automotive assemblies to hold components such as pistons, valves, and shafts in position. They can be installed quickly and easily, and are available in different sizes and thicknesses to suit various applications. Some snap rings have a locking feature to prevent accidental removal, while others are designed for easy disassembly and reassembly.
8. Cotter Pins
Cotter pins are thin, metal pins with a split end. They are used to secure bolts, nuts, or other fasteners in place to prevent them from loosening or coming apart. Cotter pins are inserted through a hole in the bolt or nut and then bent to lock it in position. They are often used in applications where safety is critical, such as in the suspension system or braking system of a vehicle. In addition to their locking function, cotter pins can also serve as a visual indicator of whether a fastener has been properly secured.
9. Threaded Inserts
Threaded inserts are used to provide a strong and durable threaded connection in materials that may not have sufficient strength or thread-holding ability on their own. They are typically made of metal, such as brass or stainless steel, and are inserted into a pre-drilled hole. Threaded inserts can be used in plastic components, aluminum parts, or other materials that are prone to stripping or wearing of the threads. There are different types of threaded inserts, including press-fit inserts, which are pressed into the hole using a special tool, and self-tapping inserts, which can be screwed into place without the need for a pre-tapped hole.
10. Studs
Studs are threaded fasteners that have threads on both ends. One end is screwed into a tapped hole in a component, while the other end protrudes and is used to attach another part using a nut. Studs are often used in applications where a more secure and reliable connection is required, such as in the engine block to attach components like the cylinder head or intake manifold. They provide better alignment and distribution of the clamping force compared to using bolts alone. Studs can also be used in situations where frequent disassembly and reassembly are necessary, as they reduce the wear and tear on the tapped holes.
11. Blind Rivets
Blind rivets, also known as pop rivets, are a type of rivet that can be installed from one side of the material, making them suitable for applications where access to the back of the joint is limited. They consist of a rivet body, a mandrel, and a setting tool. To install a blind rivet, the rivet is inserted into a pre-drilled hole, and the setting tool is used to pull the mandrel, which causes the rivet body to expand and form a permanent connection. Blind rivets are commonly used in automotive manufacturing for attaching interior trim, upholstery, and other components where a neat and hidden fastening solution is desired. They are available in different materials and sizes to accommodate various applications.
IV. The Value of Rapidefficient in CNC Machining Market
1. Precision and Quality
Rapid Efficient has made significant strides in enhancing the precision and quality of automotive fasteners through its advanced CNC machining techniques. The company utilizes state-of-the-art machinery equipped with high-precision sensors and advanced control systems, ensuring that each fastener is manufactured to exacting standards. For instance, in the production of bolts, the threading process is carried out with micron-level accuracy, minimizing any deviations that could affect the fit and performance of the fastener. This level of precision is crucial, especially in critical applications such as engine components, where even the slightest imperfection could lead to catastrophic failures.
In a recent case study, Rapid Efficient was tasked with manufacturing a batch of high-strength bolts for a leading automotive manufacturer. By implementing their precision machining processes, the company was able to achieve a tolerance level of within ±0.005mm, far exceeding the industry standard. This not only enhanced the overall quality of the bolts but also contributed to the improved performance and reliability of the vehicles in which they were installed.
2. Efficiency and Productivity
The adoption of innovative technologies by Rapid Efficient has led to a remarkable increase in production efficiency. Their CNC machining centers are equipped with high-speed spindles and advanced tooling systems, allowing for faster cutting speeds and reduced cycle times. For example, in the production of screws, the company has implemented a multi-axis machining process that enables simultaneous operations, significantly reducing the time required for each screw to be manufactured.
Moreover, Rapid Efficient has integrated automated material handling systems into their production lines, minimizing the need for manual intervention and further enhancing productivity. This has enabled the company to increase its production capacity by over 30% in the past year, while maintaining the highest quality standards. As a result, automotive manufacturers can rely on Rapid Efficient to meet their growing demands for fasteners in a timely and efficient manner.
3. Cost-effectiveness
Rapid Efficient’s CNC machining processes offer significant cost savings for automotive manufacturers. By optimizing the machining operations and reducing material waste, the company is able to lower the production costs of fasteners. For instance, through the use of advanced nesting algorithms, the company is able to minimize the amount of raw material required for each fastener, resulting in substantial savings.
In addition, the enhanced productivity and reduced cycle times translate into lower labor costs per unit, making Rapid Efficient’s fasteners a cost-effective choice for manufacturers. The company also offers competitive pricing without compromising on quality, providing excellent value for money. This cost-effectiveness has enabled automotive manufacturers to improve their profit margins while maintaining the highest quality standards in their vehicles.
V. Conclusion
Automotive fasteners are the unsung heroes of the automotive industry, playing a vital role in ensuring the safety and performance of vehicles. The 11 types of fasteners discussed in this article each have their unique characteristics and applications, and choosing the right one for each specific job is crucial.
Rapid Efficient’s CNC machining technology has brought significant value to the production of automotive fasteners, enhancing precision, efficiency, and cost-effectiveness. By partnering with a reliable and advanced CNC aluminum machining service provider like Rapid Efficient, automotive manufacturers can ensure the quality and reliability of their fasteners, ultimately leading to safer and more efficient vehicles.
In conclusion, whether you are an automotive enthusiast, a mechanic, or a professional in the automotive industry, understanding the different types of automotive fasteners and the value of advanced machining technologies is essential. It allows you to make informed decisions when it comes to vehicle maintenance, repair, and manufacturing, ensuring that every fastener does its job and keeps our cars running smoothly on the road.
So, the next time you take a look under the hood or work on a car project, remember the importance of these small but mighty components and the technology that goes into making them.
VI. Recommended Rapidefficient CNC Aluminum Processing Service Providers
When it comes to sourcing high-quality automotive fasteners, partnering with a reliable CNC aluminum processing service provider is essential. One such recommended provider is [Rapidefficient Company Name].
Rapidefficient has established itself as a leader in the CNC machining industry, offering a wide range of services tailored to meet the specific needs of automotive manufacturers. Their state-of-the-art facilities are equipped with advanced CNC machines that ensure precision and consistency in the production of fasteners.
With a team of highly skilled technicians and engineers, Rapidefficient is able to provide custom solutions for various automotive fastening applications. They offer competitive pricing without compromising on quality, making them a cost-effective choice for businesses looking to enhance their supply chain.
To get in touch with Rapidefficient and learn more about their CNC aluminum processing services for automotive fasteners, you can visit their official website at [www.rapidefficient.com] or contact their sales team directly at [[email protected]]. Their dedicated customer service representatives will be happy to assist you with any inquiries and provide detailed information on how they can meet your specific requirements.