I. Introduction
Corrosion is a pervasive and costly issue that affects various industries and our daily lives. It can cause damage to structures, machinery, and equipment, leading to reduced lifespan, increased maintenance costs, and even safety hazards. For example, in the automotive industry, corrosion can weaken the chassis and body of vehicles, compromising their structural integrity. In the marine sector, the corrosive nature of seawater poses a significant threat to ships and offshore structures. Therefore, the search for materials with excellent corrosion resistance has become crucial. In this article, we will explore different materials that exhibit good corrosion resistance and their applications. Additionally, we will touch upon the value of rapidefficient in the CNC machining market, which plays an important role in the production and processing of these corrosion-resistant materials.
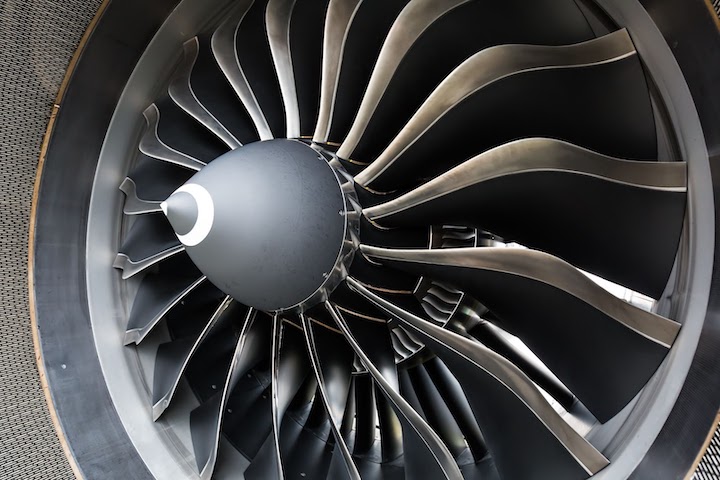
II. Understanding Corrosion
Corrosion can be defined as the deterioration of a material due to its reaction with the surrounding environment. It occurs when metals or other substances are exposed to various agents such as air, water, chemicals, and temperature changes. The most common cause of corrosion is the oxidation process, where a metal reacts with oxygen in the air to form metal oxides. For example, iron rusts when it reacts with oxygen and moisture, forming iron oxide (Fe₂O₃). This not only weakens the material but also affects its appearance and functionality.
There are different types of corrosion, including chemical corrosion and electrochemical corrosion. Chemical corrosion takes place when a metal reacts directly with a chemical substance without the involvement of an electric current. This can happen, for instance, when metals are exposed to strong acids or alkalis. Electrochemical corrosion, on the other hand, is more complex and occurs when a metal is in contact with an electrolyte, and a potential difference is created, leading to the flow of electric current and the dissolution of the metal. This type of corrosion is prevalent in many industrial and natural environments, such as in the presence of saltwater or acidic rain.
III. Factors Affecting Material Corrosion Resistance
The corrosion resistance of materials is influenced by multiple factors, including material composition, microstructure, and environmental conditions. Understanding these factors is essential for selecting appropriate materials in different applications.
A. Material Composition
The chemical elements present in a material play a significant role in determining its corrosion resistance. For example, metals like stainless steel contain chromium, nickel, and molybdenum. Chromium forms a passive oxide layer on the surface of the steel, which acts as a protective barrier against corrosion. Nickel enhances the stability of this oxide layer and also improves the resistance to acidic environments. Molybdenum, on the other hand, increases the resistance to pitting corrosion, especially in the presence of chloride ions, such as in seawater or industrial environments with salt-containing solutions.
In alloys, the combination and proportion of different elements are crucial. For instance, in some nickel-based alloys, a high nickel content provides excellent resistance to corrosion in a wide range of chemical and thermal conditions. Additionally, elements like titanium and zirconium can improve the corrosion resistance of certain materials by forming stable oxides that are highly resistant to chemical attack.
B. Microstructure
The microstructure of a material, which includes aspects like grain size, grain boundaries, and the presence of phases or inclusions, also impacts its corrosion resistance. Generally, materials with a finer grain structure tend to have better corrosion resistance. This is because finer grains offer more grain boundaries, and these boundaries can act as barriers to the diffusion of corrosive species. For example, in some metal alloys, when the grains are refined through proper heat treatment processes, the corrosion rate can be significantly reduced.
The presence of different phases within a material can either enhance or reduce its corrosion resistance. If there are second phases that are more noble (less likely to corrode) than the matrix phase, they can act as sacrificial anodes and protect the matrix from corrosion. However, if there are phases that form local electrochemical cells with the matrix and have a large potential difference, it can accelerate the corrosion process. Inclusions or impurities in the material can also serve as sites for corrosion initiation, as they may disrupt the uniformity of the structure and create areas of weakness.
C. Environmental Factors
- Temperature: An increase in temperature usually accelerates the corrosion rate. Higher temperatures can speed up chemical reactions between the material and the corrosive agents in the environment. For example, in industrial processes where materials are exposed to high-temperature steam or hot chemical solutions, the risk of corrosion is much greater compared to lower temperature conditions. In some cases, a small increase in temperature can lead to a significant increase in the rate at which metals oxidize or react with other substances in the surrounding environment.
- Humidity: Humidity affects corrosion by providing the necessary moisture for electrochemical reactions to occur. In a highly humid environment, a thin layer of water can form on the surface of the material, which can dissolve corrosive gases like oxygen and carbon dioxide, creating an electrolyte that enables the flow of electric current and subsequent corrosion. For instance, in coastal areas where the air is often saturated with moisture, metals are more prone to rusting compared to arid regions.
- pH Level (Acidity or Alkalinity): The pH of the environment has a profound impact on corrosion. In acidic environments, metals are more likely to dissolve as hydrogen ions in the acid can react with the metal atoms, causing corrosion. On the other hand, in highly alkaline environments, certain metals may also undergo chemical reactions that lead to their degradation. For example, aluminum has good corrosion resistance in a neutral pH range but can corrode rapidly in very acidic or very alkaline solutions. Different materials have different pH ranges in which they exhibit optimal corrosion resistance, and understanding this is crucial for their proper application.
- Presence of Corrosive Chemicals: The presence of specific chemicals like salts, acids, alkalis, and oxidizing agents can greatly influence corrosion. Chloride ions, for example, are notorious for causing pitting corrosion in metals like stainless steel. Industrial chemicals such as sulfuric acid, hydrochloric acid, and caustic soda can rapidly corrode materials that are not specifically designed to resist them. In chemical processing plants, the selection of materials with appropriate corrosion resistance to the chemicals being handled is of utmost importance to ensure the longevity and safety of the equipment.
By taking these factors into account, engineers and material scientists can make informed decisions when choosing materials for various applications, whether it’s in the construction industry, automotive manufacturing, or chemical processing, to minimize the impact of corrosion and ensure the durability of the structures and components.
IV. Common Corrosion Resistant Materials
A. Stainless Steel
Stainless steel is one of the most widely used corrosion-resistant materials. It contains a significant amount of chromium, which forms a passive oxide layer on the surface, protecting the underlying metal from corrosion. The chromium content is typically at least 10.5%, and in some stainless steel grades, it can be even higher. For example, in austenitic stainless steels like 304 and 316, the chromium content is around 18% and 16-18% respectively, along with nickel and other alloying elements. 304 stainless steel is commonly used in kitchen appliances, food processing equipment, and architectural applications due to its good corrosion resistance in normal environments. 316 stainless steel, with the addition of molybdenum, has enhanced resistance to pitting and crevice corrosion, making it suitable for marine environments and chemical processing plants where it is exposed to chloride-containing solutions.
Ferritic stainless steels, with a chromium content ranging from 12% to 30%, are known for their excellent resistance to stress corrosion cracking and are often used in automotive exhaust systems and some household applications. Martensitic stainless steels, while having high strength, have relatively lower corrosion resistance compared to austenitic and ferritic stainless steels and are typically used in applications where strength is a primary concern, such as in cutlery and some mechanical parts.
B. Aluminum and Its Alloys
Aluminum is a lightweight metal with good corrosion resistance, especially in the form of alloys. It forms a thin oxide layer on its surface, which provides a certain degree of protection. Aluminum alloys are widely used in the aerospace industry due to their low density and good strength-to-weight ratio. For instance, the 2000 series and 7000 series aluminum alloys are commonly used in aircraft structures. The 2024 alloy has high strength and is used for components such as wings and fuselage frames, while the 7075 alloy, with even higher strength, is used in critical parts where high stress is involved.
In the automotive industry, aluminum alloys are used to reduce vehicle weight and improve fuel efficiency. They are also used in the construction of window frames, doors, and siding in the building industry due to their corrosion resistance and ease of fabrication. Additionally, aluminum is used in the packaging industry for cans and foils because of its ability to protect the contents from oxidation and corrosion.
C. Titanium and Its Alloys
Titanium and its alloys possess outstanding corrosion resistance, high strength, and excellent biocompatibility. They are widely used in the medical field for implants such as hip replacements, dental implants, and surgical instruments. The titanium alloy Ti-6Al-4V is one of the most commonly used in medical applications due to its good combination of strength and corrosion resistance. In the aerospace industry, titanium alloys are used in aircraft engines and structural components that require high strength and resistance to extreme temperatures and corrosive environments.
Titanium’s corrosion resistance is attributed to the formation of a stable oxide layer on its surface. This oxide layer is highly resistant to chemical attack, even in harsh environments such as seawater and acidic solutions. In the marine industry, titanium is used for components in offshore oil platforms and ship propellers, where it can withstand the corrosive effects of saltwater.
D. Nickel-Based Alloys
Nickel-based alloys are known for their excellent resistance to high temperatures and corrosive environments. They contain significant amounts of nickel along with other elements such as chromium, molybdenum, and tungsten. For example, the Inconel series of alloys, such as Inconel 625 and Inconel 718, are widely used in the aerospace and power generation industries. Inconel 625 has excellent resistance to pitting and crevice corrosion and is used in gas turbines, chemical reactors, and marine applications. Inconel 718, with its high strength and good fatigue resistance, is used in aircraft engine components and high-temperature fasteners.
Another nickel-based alloy, Hastelloy, is renowned for its resistance to a wide range of corrosive chemicals, including acids and alkalis. Hastelloy C-276 is often used in chemical processing plants where it is exposed to aggressive chemicals. These nickel-based alloys are able to maintain their mechanical properties and corrosion resistance at elevated temperatures, making them suitable for applications where other materials would fail.
E. Polymer Materials
Polymer materials, such as polytetrafluoroethylene (PTFE), polyethylene (PE), and polypropylene (PP), also exhibit good corrosion resistance. PTFE, commonly known as Teflon, has excellent chemical inertness and is resistant to almost all chemicals except molten alkali metals and fluorine gas. It has a very low coefficient of friction and is used in applications such as non-stick cookware, seals, and gaskets in the chemical and food industries.
Polyethylene comes in different densities, with high-density polyethylene (HDPE) having good resistance to many chemicals and being used in the production of pipes for water and gas distribution, as well as in chemical storage tanks. Polypropylene is also resistant to a variety of chemicals and is used in the manufacturing of laboratory equipment, automotive parts, and packaging materials. These polymer materials are lightweight, easy to process, and offer good corrosion resistance in specific applications, making them a cost-effective choice in many industries.
V. How to Select the Right Corrosion Resistant Material
When choosing a corrosion-resistant material for a specific application, several factors need to be considered to ensure the best performance and cost-effectiveness.
A. Consider the Application Environment
The nature of the environment in which the material will be used is a crucial factor. For industrial applications such as chemical processing plants, where there is exposure to a wide range of corrosive chemicals, materials like Hastelloy or titanium alloys might be suitable. In marine environments, stainless steel with a high molybdenum content, such as 316 stainless steel, or titanium, can withstand the corrosive effects of saltwater. In a less aggressive environment, such as indoor architectural applications, 304 stainless steel or aluminum alloys may be sufficient.
B. Evaluate the Required Mechanical Properties
In addition to corrosion resistance, the mechanical properties of the material, such as strength, hardness, ductility, and fatigue resistance, need to be taken into account. For example, in the aerospace industry, materials need to have both high strength and good corrosion resistance to withstand the extreme conditions during flight. Titanium alloys are often favored in such cases due to their excellent combination of these properties. In the automotive industry, where weight reduction is also a concern, aluminum alloys with appropriate strength and corrosion resistance are commonly used.
C. Weigh the Cost and Availability
Cost is always an important consideration. Some corrosion-resistant materials, like titanium and nickel-based alloys, can be expensive. Stainless steel and aluminum alloys are generally more cost-effective. However, the overall cost should be evaluated considering the lifespan and maintenance requirements of the material. If a more expensive material has a significantly longer lifespan and requires less maintenance, it may be a more economical choice in the long run. The availability of the material also matters, especially for large-scale projects. Commonly available materials are usually easier to source and may have shorter lead times.
D. Assess the Fabrication and Machining Requirements
The ease of fabrication and machining of the material can impact production costs and lead times. Some materials, like stainless steel, are relatively easy to machine and can be formed into various shapes. However, titanium and some nickel-based alloys can be more difficult to machine due to their high strength and hardness. Polymer materials are generally easy to process using techniques such as injection molding or extrusion, but they may have limitations in terms of temperature and chemical resistance compared to metals. For example, in the production of custom parts, the machinability of the material should be considered to ensure efficient and accurate manufacturing.
By carefully evaluating these factors, engineers and designers can select the most appropriate corrosion-resistant material for a given application, balancing performance, cost, and practicality.
VI. The Value of Rapidefficient in CNC Machining Market
Rapidefficient has emerged as a significant player in the CNC machining market, especially when it comes to processing corrosion-resistant materials. With its advanced technology and expertise, it offers several advantages that set it apart from its competitors.
In terms of precision machining, Rapidefficient utilizes state-of-the-art CNC machines equipped with high-precision spindles and advanced control systems. This enables the production of parts with extremely tight tolerances, which is crucial for many applications where corrosion-resistant materials are used. For example, in the aerospace industry, components made from titanium alloys or nickel-based alloys require precise dimensions to ensure proper fit and function. Rapidefficient’s machining capabilities ensure that these parts are manufactured to the exact specifications, minimizing the risk of errors and rework.
The company also prides itself on its efficient production processes. By optimizing tool paths and cutting parameters, Rapidefficient is able to reduce machining time significantly. This not only increases productivity but also lowers production costs. In a competitive market, this efficiency can make a significant difference for customers, allowing them to bring their products to market faster and at a more competitive price. For instance, in the production of stainless steel parts for the food processing industry, Rapidefficient’s efficient machining processes can help manufacturers meet tight production schedules and reduce overall manufacturing costs.
Rapidefficient also pays great attention to surface finish. Corrosion-resistant materials often require a high-quality surface finish to enhance their resistance to corrosion and improve their aesthetic appearance. The company employs specialized finishing techniques such as grinding, polishing, and coating to achieve the desired surface finish. This is particularly important in industries such as architecture and automotive, where the appearance of the finished product is as important as its functionality. For example, in the production of aluminum alloy parts for high-end automobiles, a smooth and flawless surface finish is essential to meet the strict quality standards of the automotive industry.
In addition to its technical capabilities, Rapidefficient offers excellent customer service. The company works closely with its clients to understand their specific requirements and provides customized solutions. This includes providing technical advice on material selection, machining processes, and finishing options. The company also has a reliable supply chain, ensuring the timely delivery of raw materials and finished products. This level of customer service has helped Rapidefficient build a strong reputation in the market and establish long-term relationships with its clients.
Overall, Rapidefficient’s value in the CNC machining market lies in its ability to combine precision machining, efficient production processes, high-quality surface finishes, and excellent customer service. Whether it’s processing stainless steel, aluminum alloys, titanium alloys, or other corrosion-resistant materials, Rapidefficient has the expertise and resources to meet the diverse needs of its customers and contribute to the success of their projects.
VII. Conclusion
In conclusion, choosing the right corrosion-resistant material is essential for the durability and performance of various structures and equipment. Stainless steel, aluminum and its alloys, titanium and its alloys, nickel-based alloys, and polymer materials are among the commonly used corrosion-resistant materials, each with its unique properties and applications. By considering factors such as the application environment, mechanical properties, cost, and fabrication requirements, engineers and designers can make informed decisions to select the most suitable material for their specific needs.
Rapidefficient plays a valuable role in the CNC machining market, especially in processing these corrosion-resistant materials. Its precision machining capabilities, efficient production processes, high-quality surface finishes, and excellent customer service make it a preferred choice for many industries. Whether it’s for aerospace, automotive, marine, or chemical processing applications, Rapidefficient has the expertise and resources to deliver high-quality machined parts that meet the strictest standards.
If you are in need of CNC machining services for corrosion-resistant materials, don’t hesitate to reach out to Rapidefficient. Their team of experts will be happy to assist you in finding the best solutions for your projects. With the right materials and machining partner, you can ensure the long-term success and reliability of your products and operations.
VIII. Recommended Rapidefficient CNC Aluminum Processing Service Provider
Rapidefficient is a leading CNC aluminum processing service provider that has been serving various industries with high-quality machining solutions. Their state-of-the-art facility is equipped with advanced CNC machines and a team of highly skilled technicians who are dedicated to delivering precision parts with excellent surface finishes.
The company offers a wide range of services, including milling, turning, drilling, and grinding, to meet the diverse needs of their clients. They have extensive experience in processing aluminum alloys for applications in the aerospace, automotive, electronics, and medical industries. Whether it’s producing complex components for aircraft engines or high-precision parts for electronic devices, Rapidefficient has the expertise and capabilities to handle the job.
One of the key advantages of choosing Rapidefficient is their commitment to quality control. They implement strict quality assurance procedures at every stage of the production process to ensure that each part meets the highest standards. Their advanced inspection equipment allows them to detect even the slightest defects and make necessary adjustments in a timely manner.
In terms of turnaround time, Rapidefficient is known for its efficiency. They understand the importance of meeting deadlines in today’s competitive business environment and strive to deliver orders on time without compromising on quality. Their streamlined production processes and optimized machining strategies enable them to reduce production lead times and increase overall productivity.